
主要作者:Yu Mao,Hui Chen,Jun Xiong*
第一单位:西南交通大学
发表期刊:Additive Manufacturing
原文链接:https://doi.org/10.1016/j.addma.2024.104419
研究背景
1.铝合金增材制造关键挑战
·随着航空航天、国防等高科技领域的快速发展,研发高强度铝合金替代传统合金已成为当前的研究热点。传统的铝合金减材制造难以满足这些领域对轻量化日益增长的需求。大多数部件具有复杂的几何结构,铝合金的整体成形通常非常困难。
·WLAM中大的温度梯度使得铝合金部件的微观结构呈择优取向的粗大柱状晶,导致沉积件具有高的热敏感性和各向异性。此外溶质元素偏析形成的弥散分布的二次相使得沉积件具有较高的裂纹敏感性。因此,细化晶粒和抑制溶质元素偏析是改善铝合金激光填丝增材构件力学性能的重要途径。
·在液态金属凝固过程中,调节晶粒的形核和生长是抑制柱状晶粒形成的理想途径。其中,优化工艺参数可以抑制铝合金柱状晶粒的生长,但性能改善有限。后处理在细化晶粒的同时也增加了部件的制造周期、成本和设备复杂性。添加形核剂可以有效细化晶粒,但成核速率受到颗粒尺寸、熔体过冷和颗粒团聚的影响。因此,如何有效地使成核颗粒均匀扩散到沉积层的各个区域仍然是一个有待解决的问题。
2.增材过程原位微合金化技术创新
提出基于光束调制的增材过程原位微合金化新方法:
·方法:向振荡激光填丝增材制造Al-Cu合金中加入了稀土元素Sc,通过Sc的原位微合金化实现晶粒细化。
·目标:制备的构件无需后处理即可获得较高的强度和延伸率。为铝合金微合金化提供了新的视角,为激光增材制造高强度铝合金提供了理论基础。
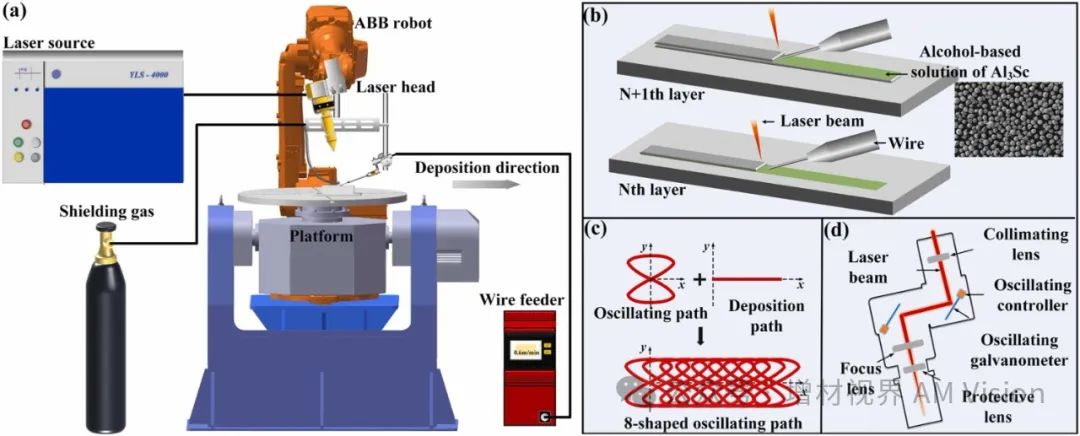
Fig.1 Schematic diagrams of equipment
研究方法
1.材料与方法
·材料:2319铝合金丝材、2219铝合金基板
·工艺参数:激光功率2400 W, 沉积速度9 mm/s, 送丝速度1.2m/min,振荡频率60 Hz,振荡幅值2.5 mm。
2.Sc的原位合金化策略
·在第N+1层沉积前,将含有5 wt % Al3Sc纳米颗粒的醇基溶液均匀涂覆在第N层沉积层表面。重复上述沉积过程,直到薄壁件成形。
3.微观组织表征和力学性能测试
·使用超景深显微镜对薄壁件宏观形貌进行观察,采用OM、EBSD、SEM等多尺度表征方法对Al-Cu合金和Al-Cu-Sc合金的微观结构进行表征,通过显微硬度试验和拉伸试验对薄壁件的力学性能进行评估。
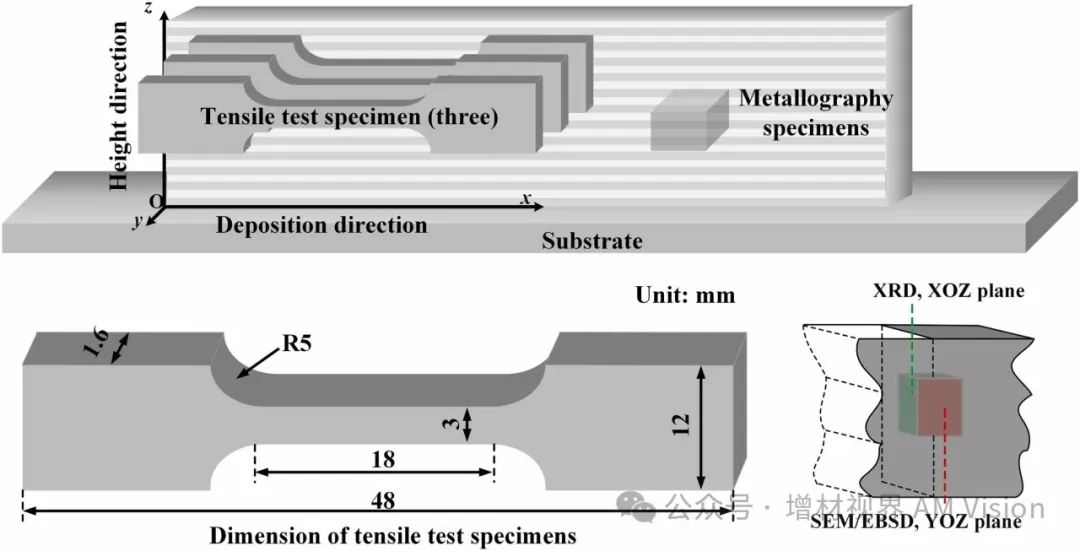
Fig.2 Positions diagram and dimensions of the specimens
研究结果
1.薄壁件几何特征
对Al-Cu合金和Al-Cu-Sc合金的宏观形貌观察后发现,Al-Cu合金的侧壁表面粗糙,有许多深度不一致的凹陷,表面粗糙度为24.2 μm。Al-Cu-Sc合金侧壁微观形貌光滑平整,无明显凹陷,表面粗糙度为13.4 μm。因此,Sc的原位微合金化有利于提高Al-Cu-Sc合金薄壁件的表面质量。

Fig.3 Surface morphologies of thin-walled components fabricated by O-WLDED
2.晶粒取向及尺寸
Al-Cu合金的OZ中等轴晶和柱状晶交替分布,RZ中孪生枝晶择优取向明显。添加Sc后,Al-Cu-Sc合金的OZ中未发现孪生枝晶,RZ的晶粒形貌均匀,取向随机。EBSD结果表明:Sc的原位微合金化能有效促进柱状晶向等轴晶转变(CET)行为,抑制孪生枝晶的形成。
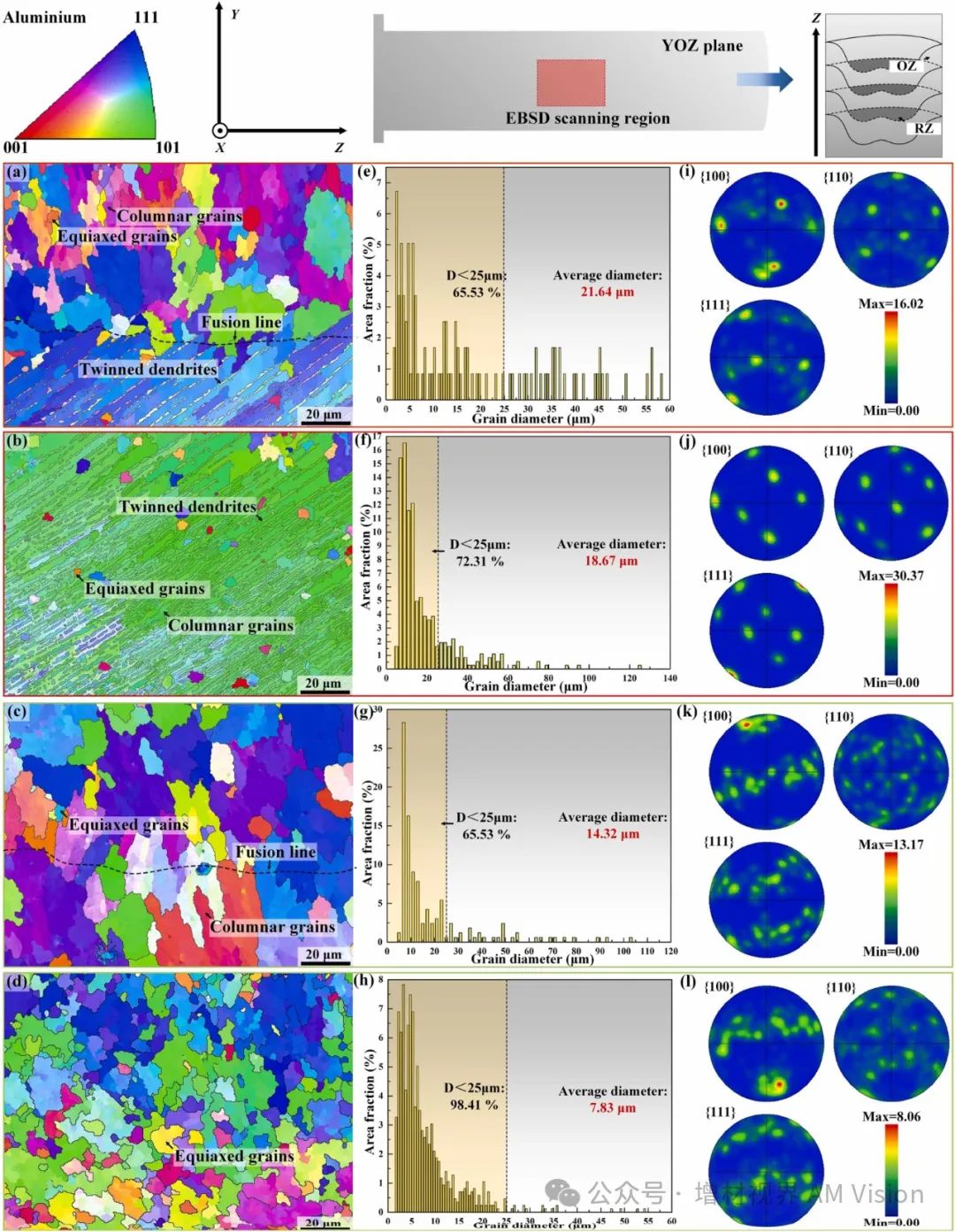
Fig.5 IPF, grain diameter distribution, and PF of the deposited specimens
3.Sc的原微合金化促进CET转变机制
Sc促使N+1层熔池底部固-液界面降低N层中RZ的形核能,导致RZ凝固过程中形成细晶区。
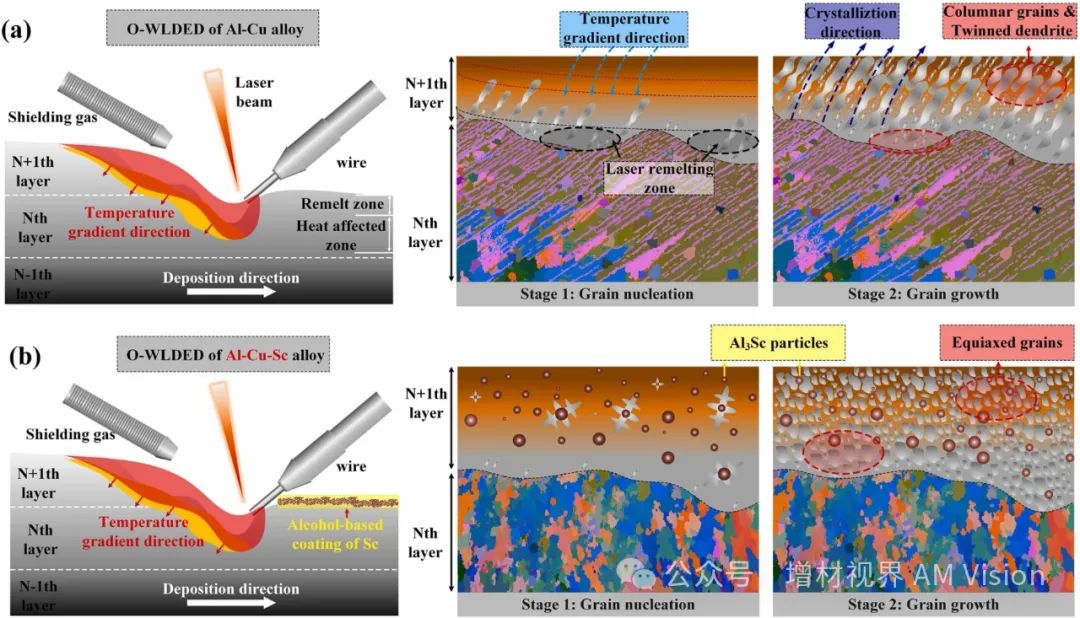
Fig.6 Schematic diagram of microstructure evolution
4.位错及大小晶界分布
Al-Cu-Sc合金与Al-Cu合金相比,具有更低的应力,更高的位错密度和更多的小角度晶界。
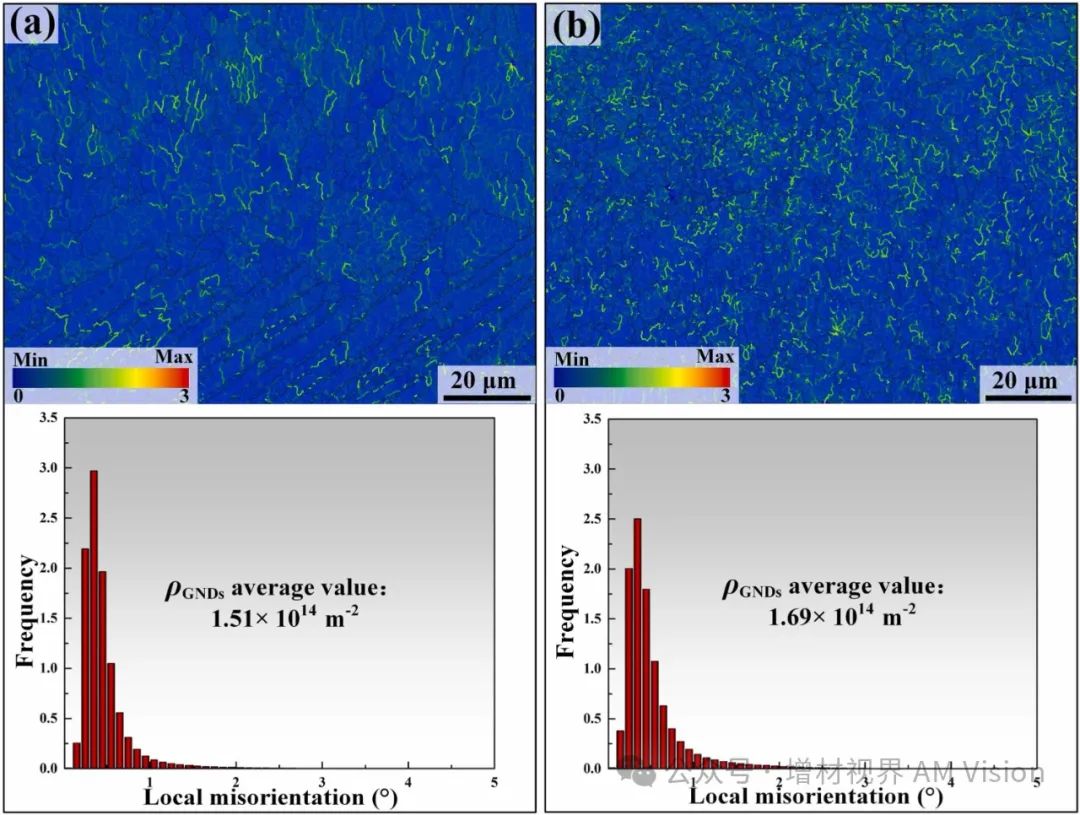
Fig.7 KAM maps and local misorientation distribution
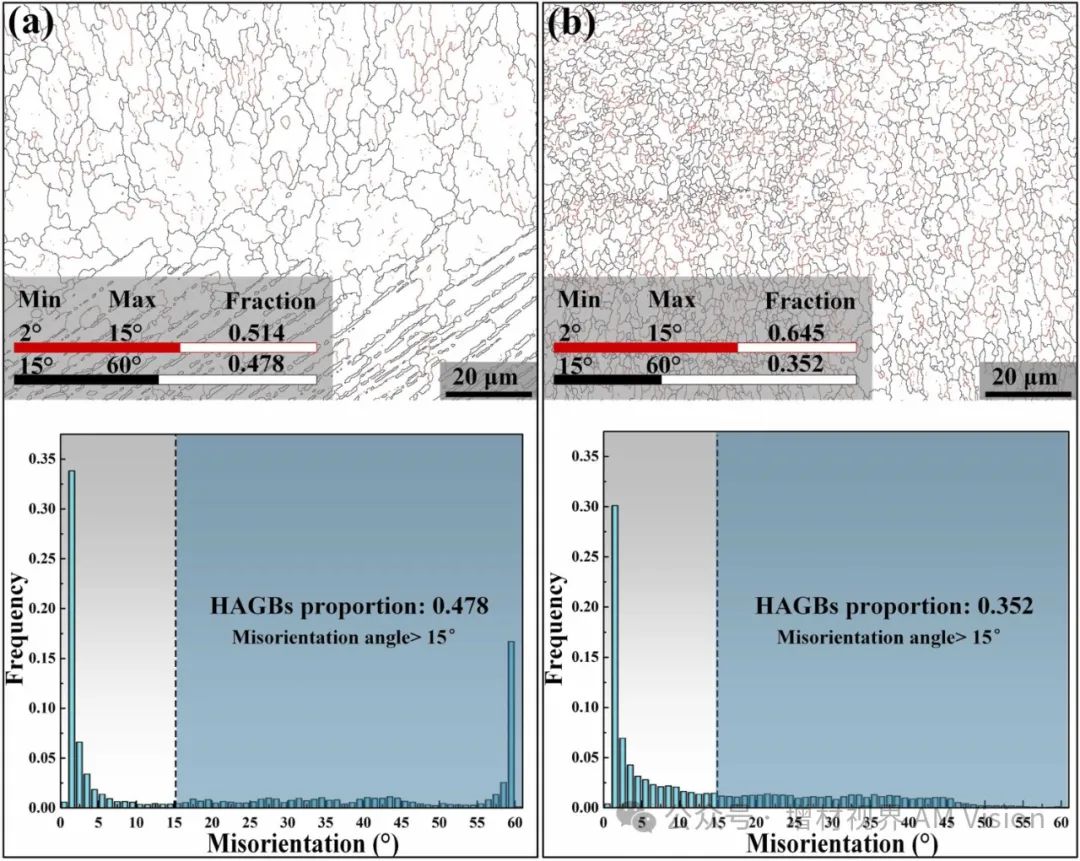
Fig.8 Distribution of LAGBs and HAGBs
5.第二相分布
Sc能有效抑制Cu的偏析并阻止其向晶界扩散,降低θ-Al2Cu和θ′-Al2Cu的含量。
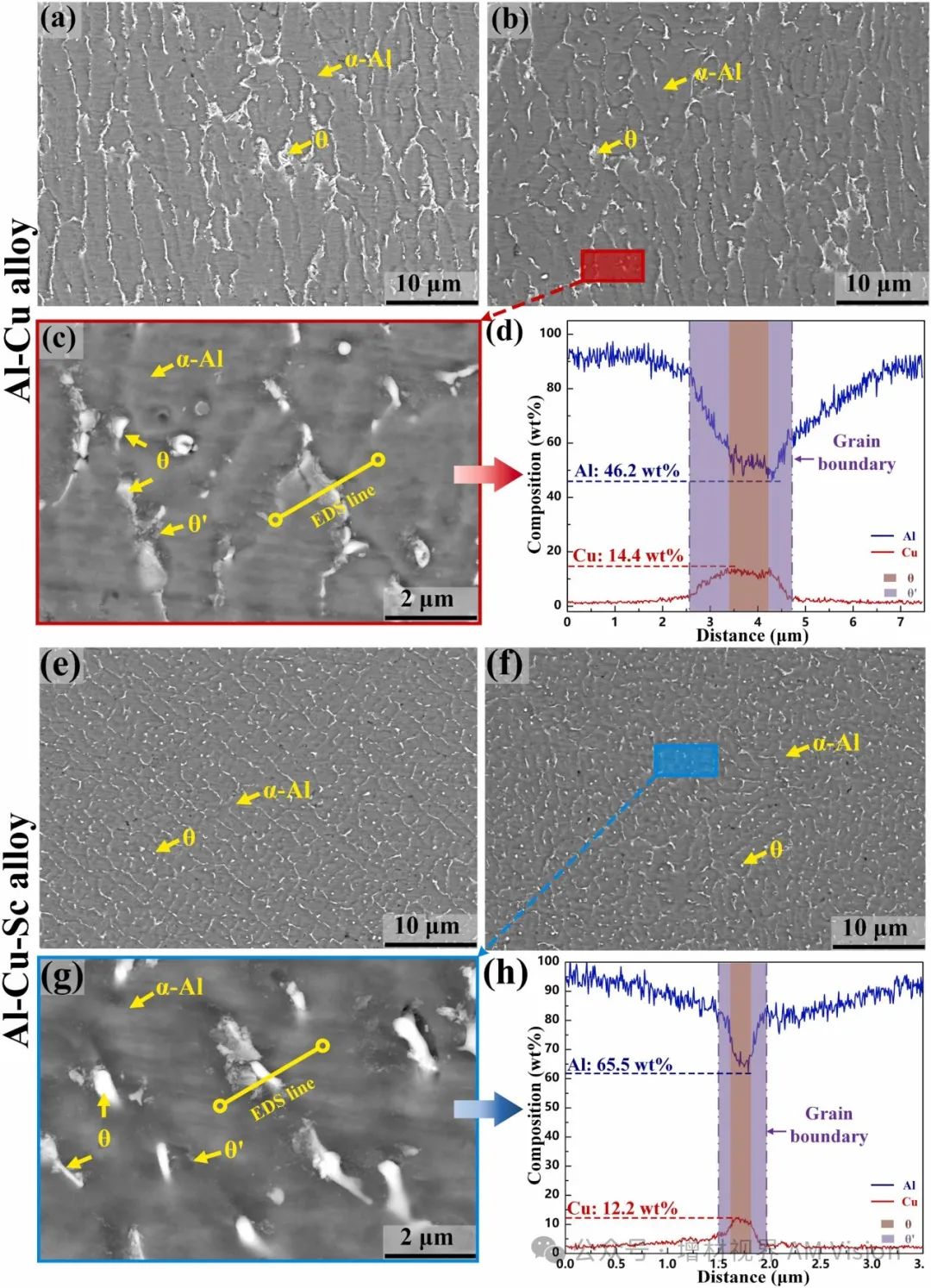
Fig.10 SEM-BSE images and EDS line scan results of the deposited specimens
6.合金元素分布
·Al-Cu合金:Cu元素在晶界处偏析,形成连续的二次相。Mg、Mn、Ti元素均匀分布在α-Al基体中;
·Al-Cu-Sc合金:Sc元素均匀分布在α-Al相中,未发生偏析。除Al3Sc外,还可能形成Al3Sc金属间化合物和弥散体;
·激光束振荡促进熔池流动,形成均匀分布的对流,能有效抑制Sc元素偏析。
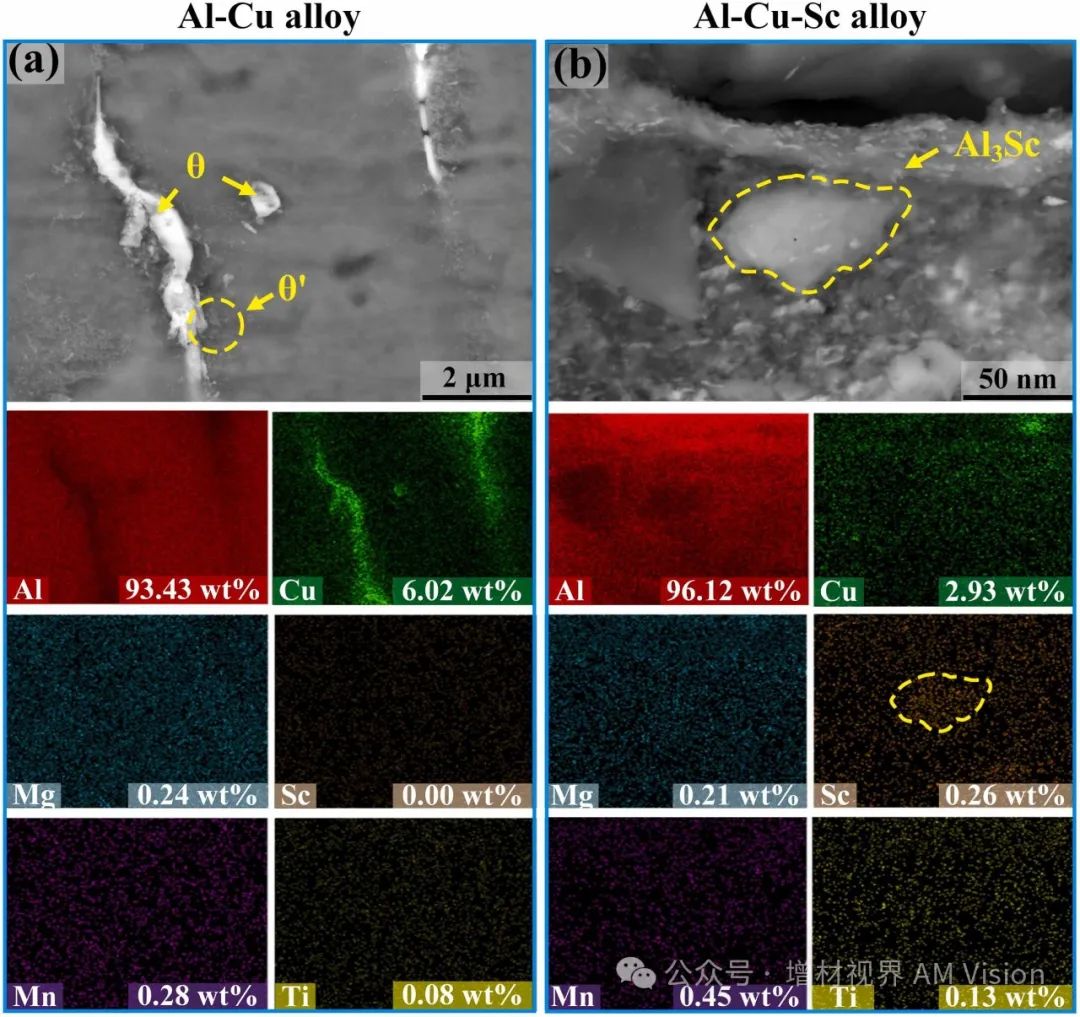
Fig.11 BSE images and element distribution maps of the deposited specimens
7.力学性能
·显微硬度:Al-Cu合金的平均显微硬度为80.3 HV,Al-Cu-Sc合金的平均显微硬度为108.5HV;
·拉伸性能:添加Sc后,Al-Cu-Sc合金的抗拉强度、屈服强度和延伸率分别提升至433 Mpa、311 Mpa和11.8%。
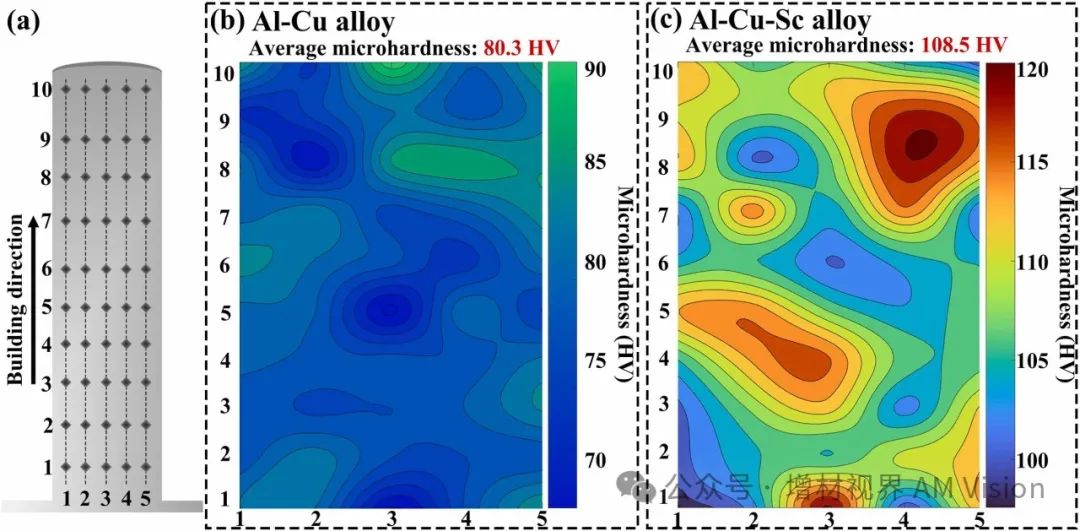
Fig.12 Two-dimensional distribution of microhardness
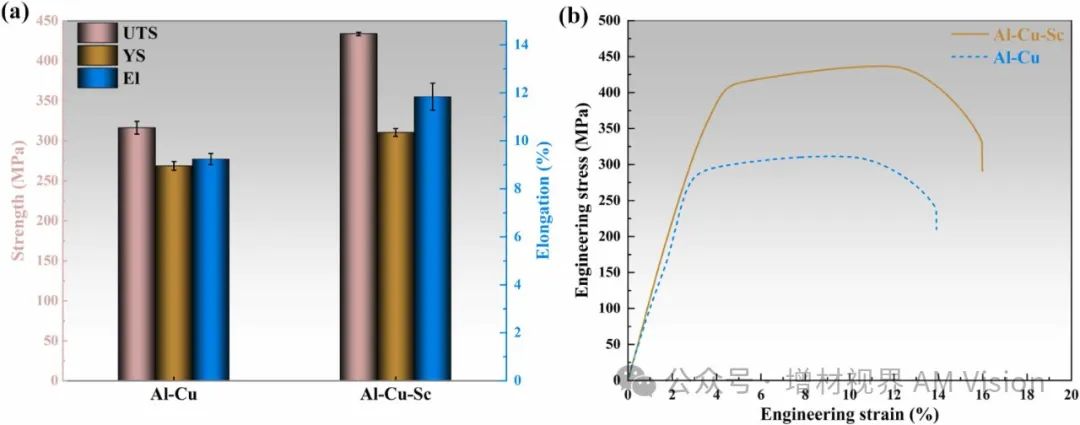
Fig.13 Tensile properties of the deposited specimens
研究结论
·Sc的原位微合金化改善了O-WLAM Al-Cu-Sc合金熔池的流动性和凝固速率,提高了Al-Cu-Sc合金的表面质量,表面粗糙度Ra从24.2降低至13.4 μm;
·添加Sc后,Al-Cu-Sc合金中的孪生枝晶消失,柱状晶转变为等轴晶。Al-Cu-Sc合金中OZ的平均晶粒尺寸从21.64 减小至14.32 μm, RZ的平均晶粒尺寸从18.67减小至7.83 μm;
·沉积试样主要由α-Al相和θ-Al2Cu相组成。从Al基体中析出的Al3Sc颗粒抑制了固溶元素Cu的偏析并阻止其向晶界扩散,从而降低了θ-Al2Cu和θ′-Al2Cu的含量。