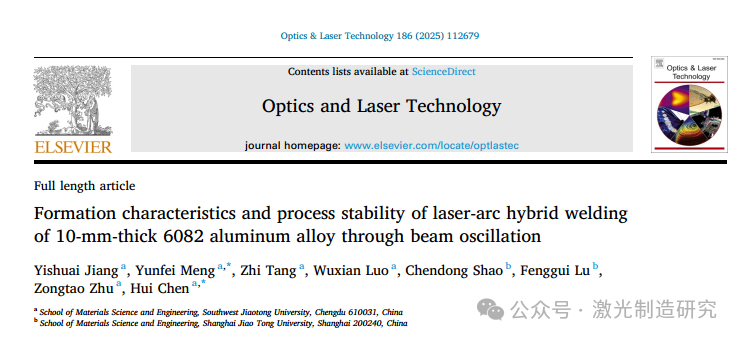
导读
在大厚度铝合金的高功率激光-电弧复合焊接中,由于激光小孔的周期性塌陷和熔池的剧烈波动,容易出现成形不良和工艺不稳定。采用功率高达8.0 kW、频率(f)从0到500 Hz变化的振荡激光器来解决10mm厚铝合金的复合焊接问题。结果表明,与非振荡复合焊接相比,在f = 500 Hz下的激光振荡将焊缝孔隙率从5.1 %降低到0.1%;此外,熔深从8.9降低到3.8 mm。当f在300至400 Hz范围内时,复合焊缝保持了高熔深和低孔隙率之间的平衡。增加f不仅使激光小孔的深宽比从5.5降低到2.3,而且使塌陷频率从652降低到253 Hz,从而提高了复合焊接的稳定性。尽管焊接接头的所有显微组织在焊缝中心呈现等轴晶,在熔合线附近呈现胞状枝晶,但f的增加使焊缝中心显微组织细化了14.0 %,等轴晶的比例从45 %增加到57 %。基于激光与电弧的相互作用、激光小孔的动态变化过程以及熔池的流动演化,分析了复合焊接过程中激光振荡的改善机理。
主要图表

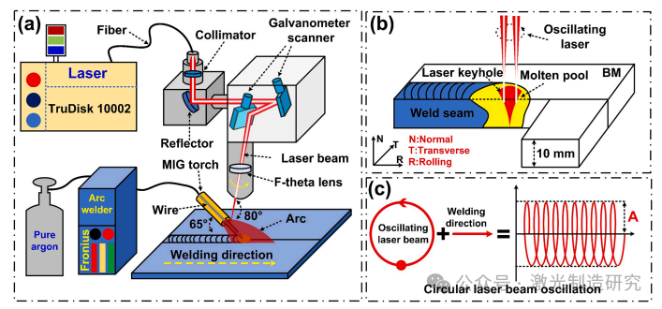
图1 OLAHW实验装置和光束振荡模式的示意图:(a)实验装置,(b)OLA HW的配置图,以及(c)圆形光束振荡模式

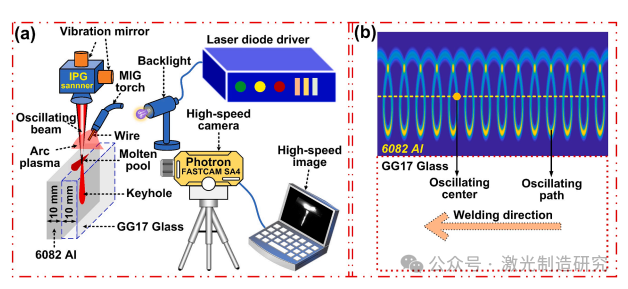
图2用高速摄像机观察小孔和气泡的示意图:(a)概述和(b)激光点的位置图。
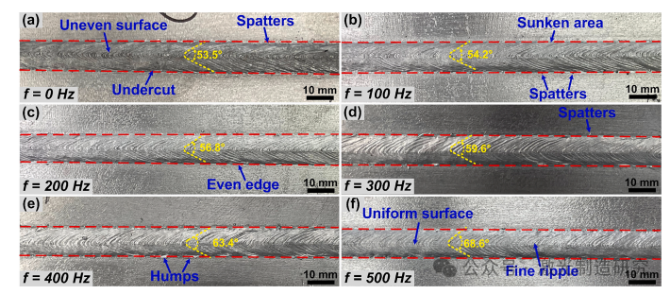
图3 不同f对焊缝表面形态的影响:(a) f = 0赫兹,(b) f = 100赫兹,(c) f = 200赫兹,(d) f = 300赫兹,(e) f = 400赫兹,以及(f) f = 500赫兹。
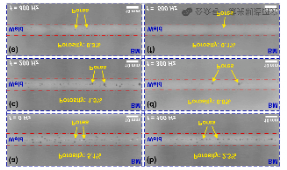
图4 x射线无损检测结果显示了不同频率下焊缝的孔隙率:(a) f = 0赫兹,(b) f = 100赫兹,(c) f = 200赫兹,(d) f = 300赫兹,(e) f = 400赫兹,以及(f) f = 500赫兹。
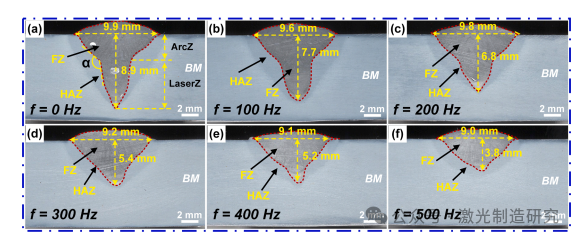
图5 不同f值对焊缝横截面宏观结构的影响:(a) f = 0赫兹,(b) f = 100赫兹,(c) f = 200赫兹,(d) f = 300赫兹,(e) f = 400赫兹,以及(f) f = 500赫兹。
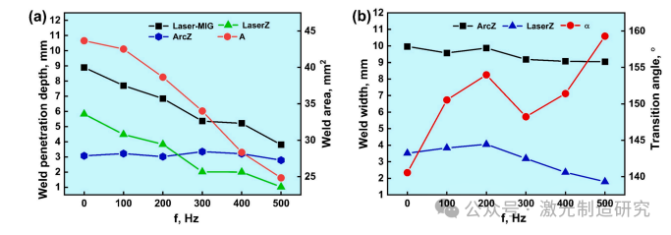
图6 不同f对焊缝横截面宏观结构影响的统计结果:(a)焊缝熔深和焊缝面积,以及(b)焊缝宽度和过渡角。
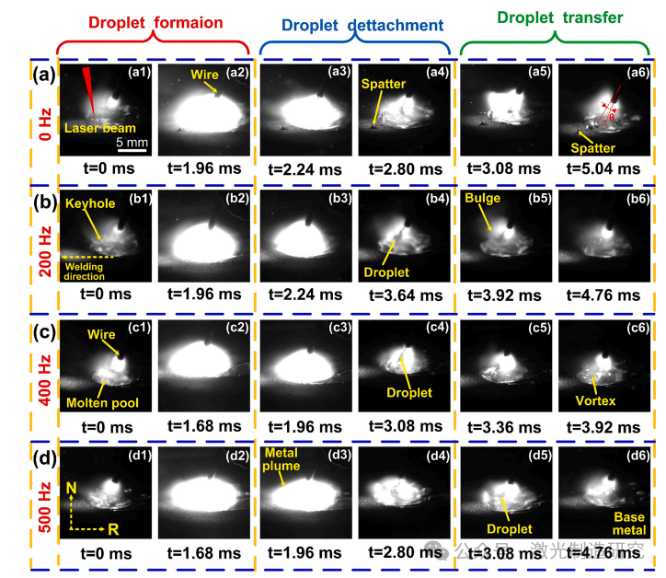
图7 混合焊接期间熔滴过渡过程的高速摄像机观察:(a)无振动,(b) f = 200 Hz,(c) f = 400 Hz,和(d) f = 500 Hz。
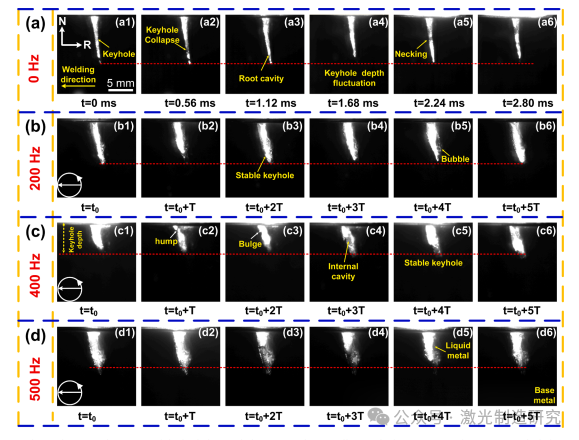
图8 小孔形态的高速摄像机观察:(a)无振荡,(b) f = 200赫兹,(c) f = 400赫兹,和(d) f = 500赫兹。
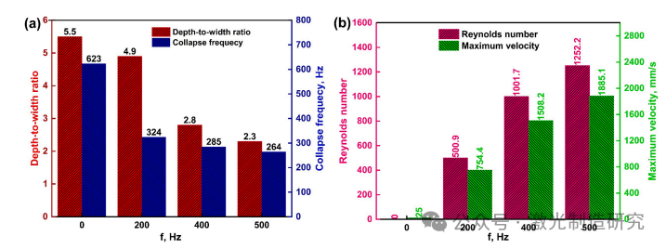
图9 小孔稳定性的统计分析:(a)小孔深宽比和小孔破裂频率,以及(b)雷诺数和最大速度。
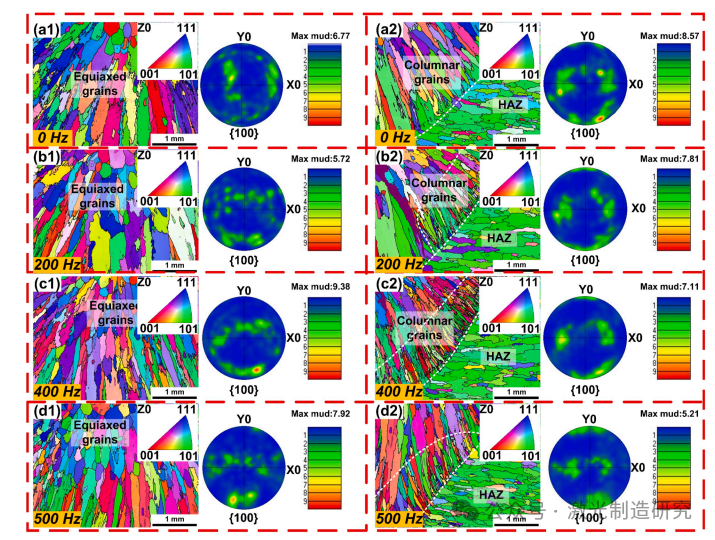
图10 在0、200、400和500 Hz下,焊缝中心和FZ与热影响区之间边界的EBSD试验结果的IPF着色图:(a1-D1)焊缝中心和(a2-D2)FZ与热影响区之间的边界。
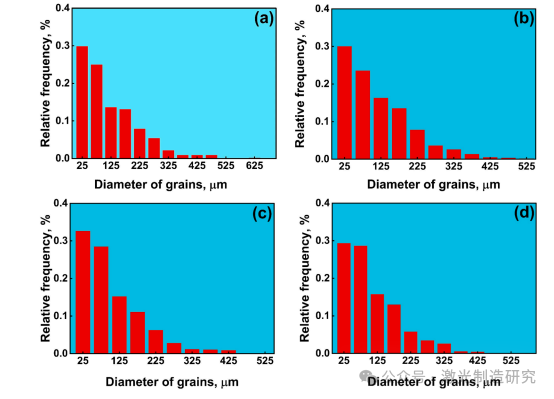
图11 焊接区的粒度分布统计:(a)无振动,(b) f = 200赫兹,(c) f = 400赫兹,以及(d) f = 500赫兹。
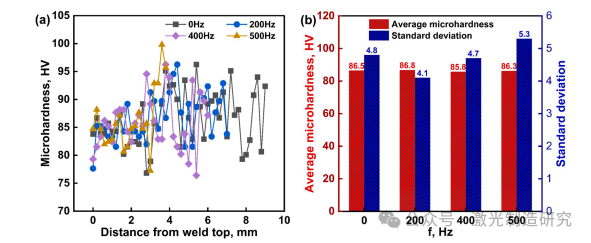
图12 焊缝显微硬度的统计分析:(a)显微硬度分布和(b)平均显微硬度。
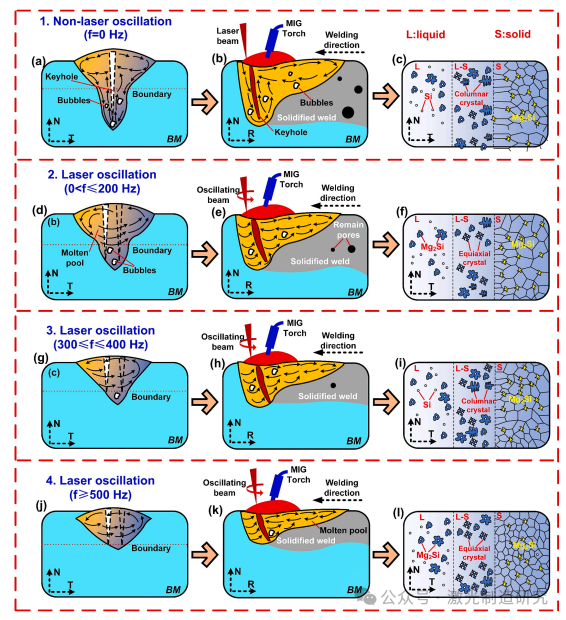
图13 激光束振荡对激光-电弧复合焊接成形特性和过程稳定性的影响机理。
主要结论
1.高频束振荡用于10mm厚的6082铝合金的LAHW。将振荡频率(f)从0增加到500 Hz,不仅将激光小孔的塌陷频率从652降低到253 Hz,而且将焊缝孔隙率从5.1 %降低到0.1 %。焊缝的熔深从8.9下降到3.8 mm。当f在300至400 Hz范围内时,复合焊缝保持了高熔深和低孔隙率之间的平衡。
2尽管所有焊接接头的显微组织在焊缝中心呈现等轴晶,在熔合线附近呈现胞状枝晶,但f的增加使焊缝中心的显微组织细化了14.0 %,120.4到103.6微米,并且将等轴晶粒的比例从45 %增加到57 %。显微硬度分布的均匀性随着f从0增加到400 Hz而提高,但是当f连续增加到500 Hz时降低。
3光束振荡改善激光-电弧复合焊接成形特性和工艺稳定性的机理如下:振荡激光使小孔的深宽比从5.5减小到2.3,并增大了上下熔池之间的过渡角(α),从而有效地改善了小孔的稳定性,降低了小孔塌陷导致气泡形成的几率。激光束的振荡频率越高,激光小孔对熔体流动的搅拌作用越大,这有利于捕获熔池中的气泡并抑制气孔的形成。
主要信息
Formation characteristics and process stability of laser-arc hybrid welding of 10-mm-thick 6082 aluminum alloy through beam oscillation
https://doi.org/10.1016/j.optlastec.2025.112679