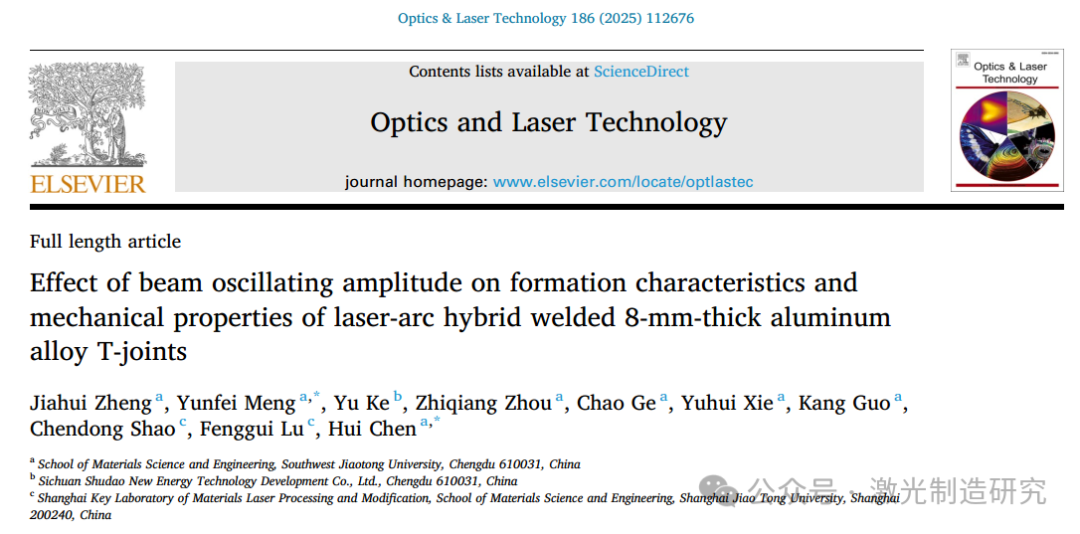
导读
针对8 mm厚铝合金T型接头激光-电弧复合焊接存在的稳定性差、气孔率高等问题,采用环形振荡激光器,振荡幅度(A)在0 ~ 0.75mm范围内变化,虽然随着A的增大,焊缝熔深由11.87 mm减小到7.17 mm,上、下熔区的熔宽差减小了45%,过渡角从129.2 °增大到178.8 °。与非振荡复合焊接相比,当A值为0.75 mm时,焊缝气孔率由9.0%降低到0.4%,焊缝组织均匀性提高了1.7倍,电弧熔化区平均晶粒尺寸细化了29%,焊接接头的拉伸断裂路径从内部气孔转移到柱状枝晶附近的热影响区,使接头的抗拉强度从186.4 MPa提高到242.6 MPa,提高了30%。优化的激光振荡不仅形成了局部湍流,而且缩短了气泡的逃逸路径,从而抑制气孔形成并改善焊接机械性能。
主要图表

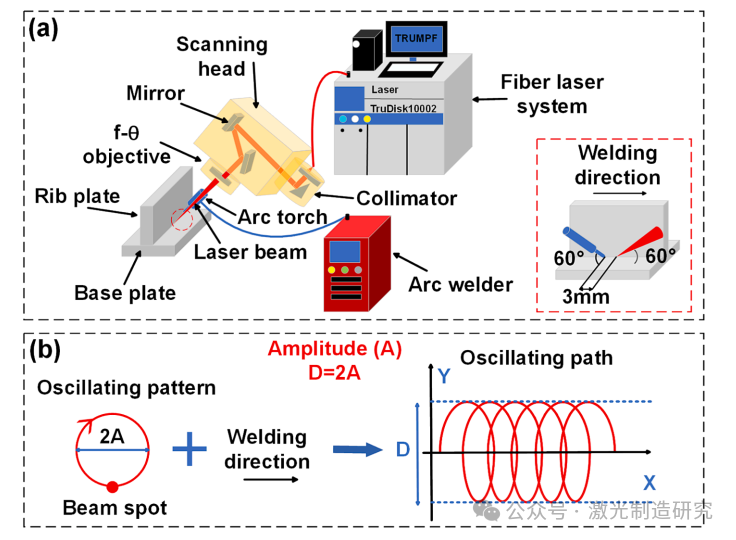
图1. T型接头振荡激光-电弧复合焊接实验装置示意图,(a)概述,(B)激光振荡模式和路径。
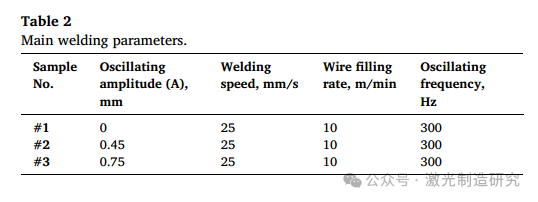
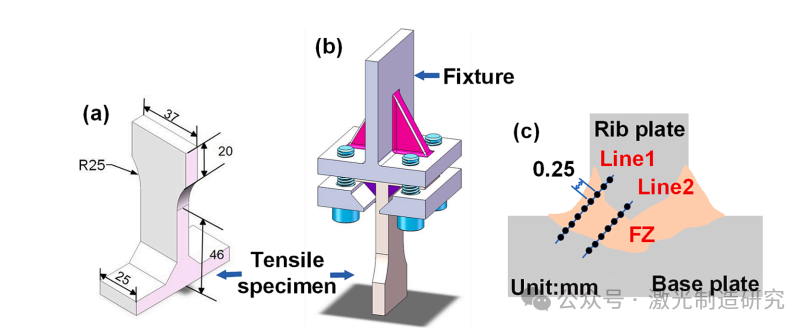
图2.拉伸和显微硬度试样示意图,(a)拉伸试样尺寸,(B)拉伸试验夹具设计,(c)显微硬度测试点。
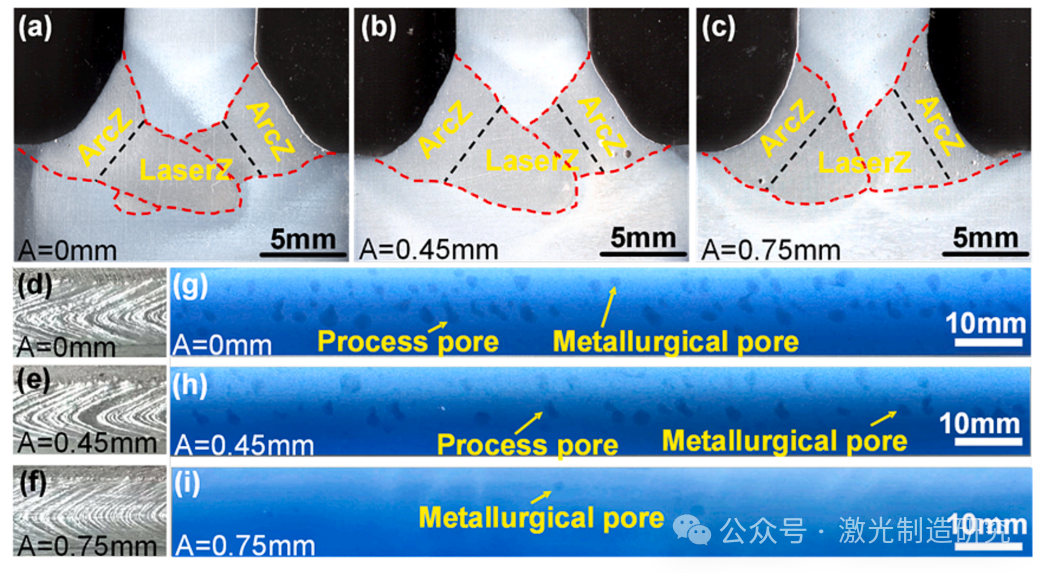
图3.振动幅度(A)对焊缝成形的影响,(a-c)横截面形貌,(d-f)表面成形,(g-i)X射线无损检测结果。
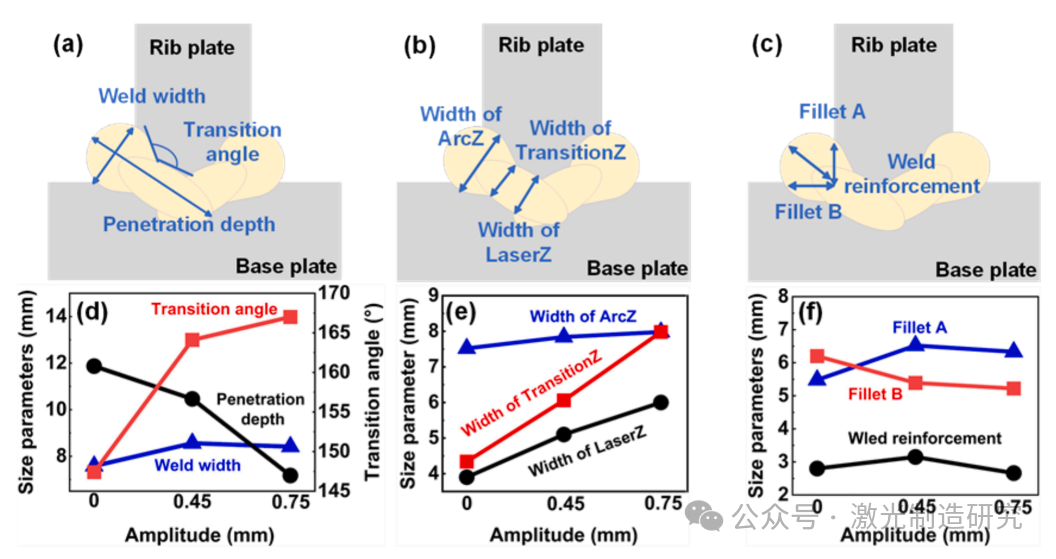
图4.振动振幅(A)对T型焊接接头尺寸参数的影响,(a-c)尺寸参数的定义,(d-f)尺寸参数与A的关系。
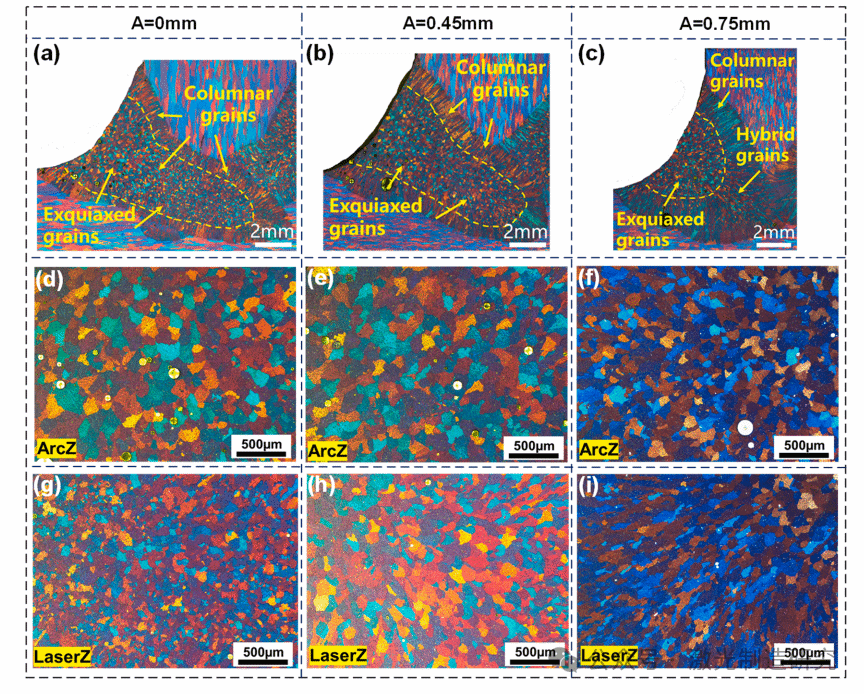
图5.不同振幅下的晶粒形貌和分布(A),(a-c)低倍放大图像,(d-f)ArcZ放大图,(g-i)LaserZ放大图。
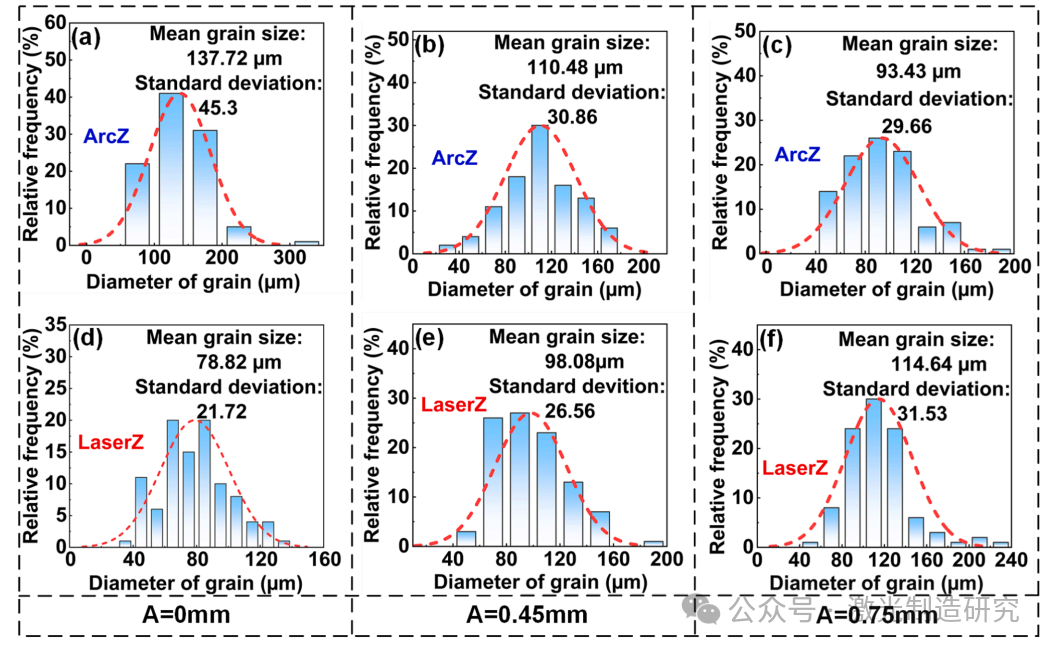
图6.振荡幅度(A)对各焊接区晶粒尺寸的影响,(a-c)ArcZ,(d-f)laserZ。
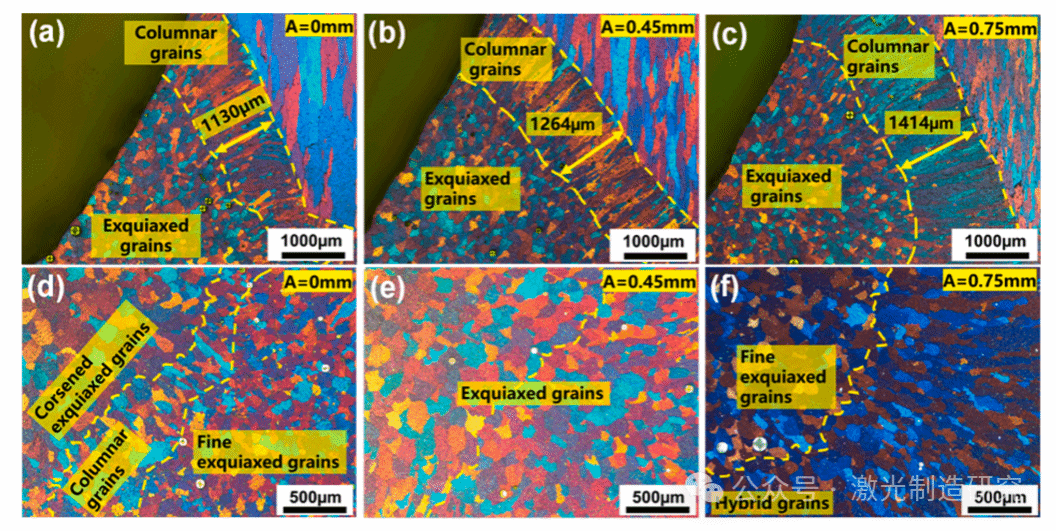
图7.不同振幅下各焊缝区的晶粒形貌和分布(A),(a-c)焊缝边缘,(d-f)过渡区Z。
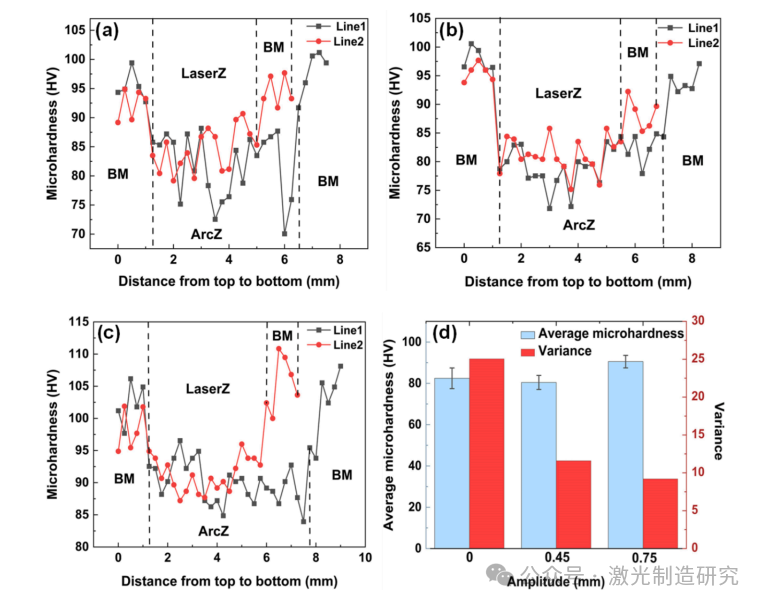
图8.不同振幅下T型接头的显微硬度分布(A),(a)A = 0 mm,(B)A = 0.45 mm,(c)A = 0.75 mm,(d)平均显微硬度及其方差。
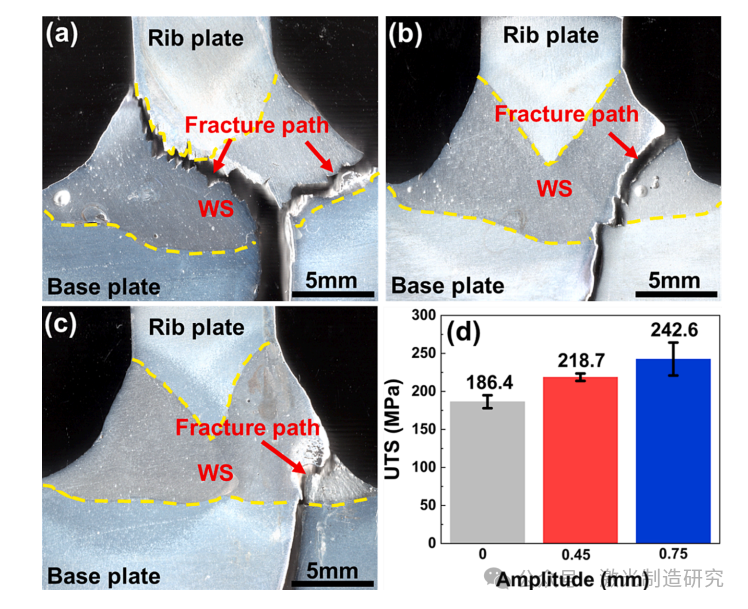
图9.不同振幅下T型接头的横截面形貌和拉伸性能(A),(a)A = 0 mm,(B)A = 0.45 mm,(c)A = 0.75 mm,(d)焊接接头的极限抗拉强度(UTS),其中WS为焊缝。
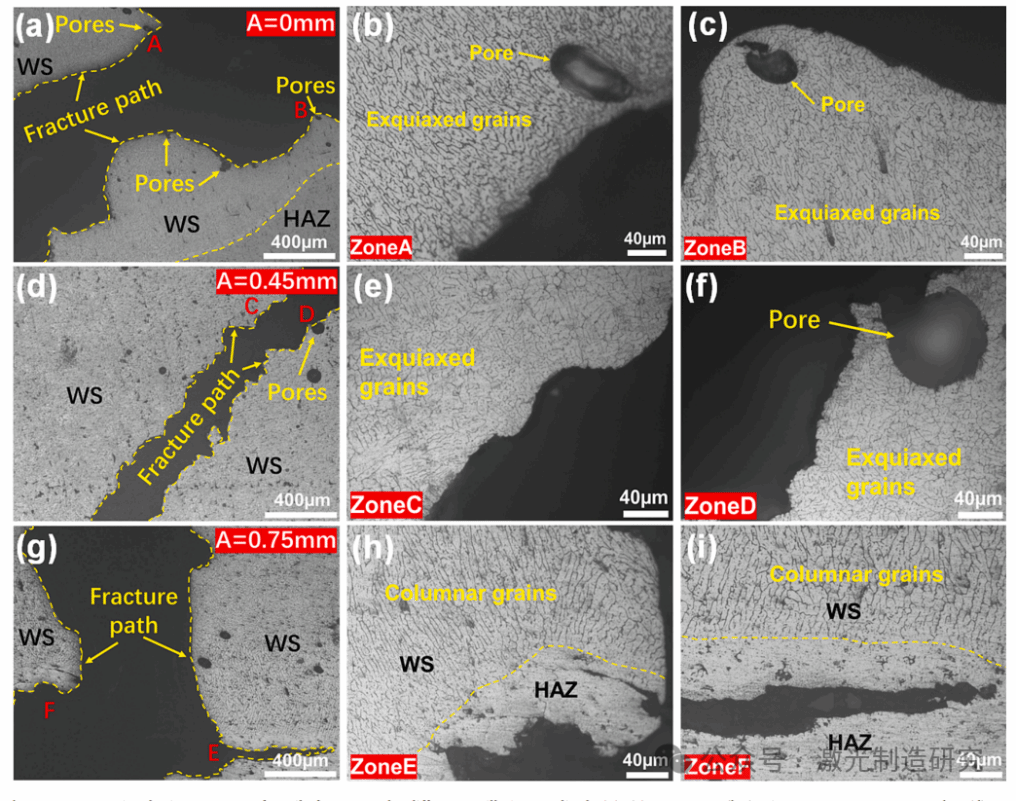
图10.不同振幅下拉伸断裂的横截面显微组织(A),(a)A = 0 mm,(b-c)A区和B区的显微组织,(d)A = 0.45 mm,(e-f)C区和D区的显微组织,(g)A = 0.75 mm,(h-i)E区和F区的显微组织。
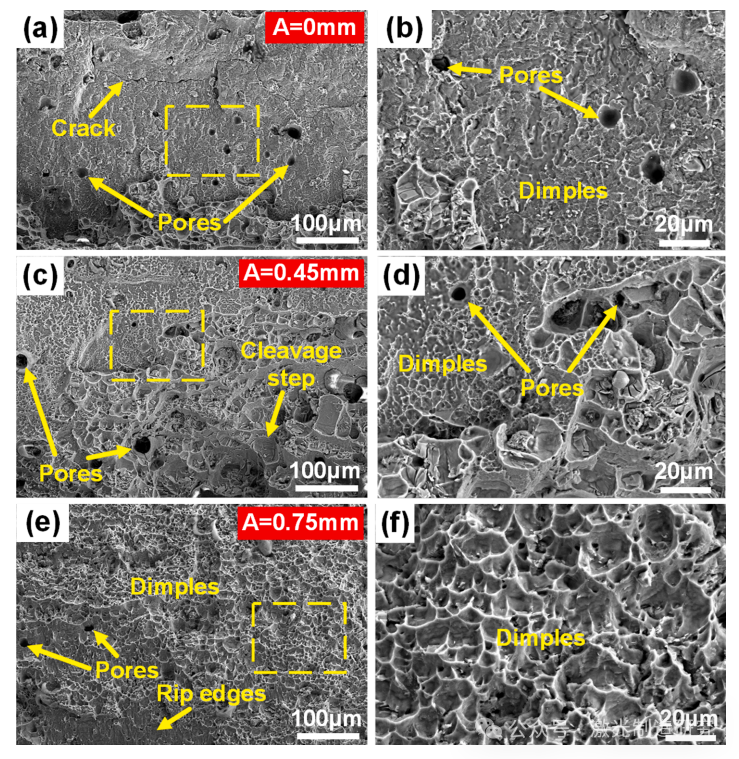
图11.不同振幅(A)下拉伸断口的表面形貌,(a-b)A = 0 mm,(c-d)A = 0.45 mm,(e-f)A = 0.75 mm。
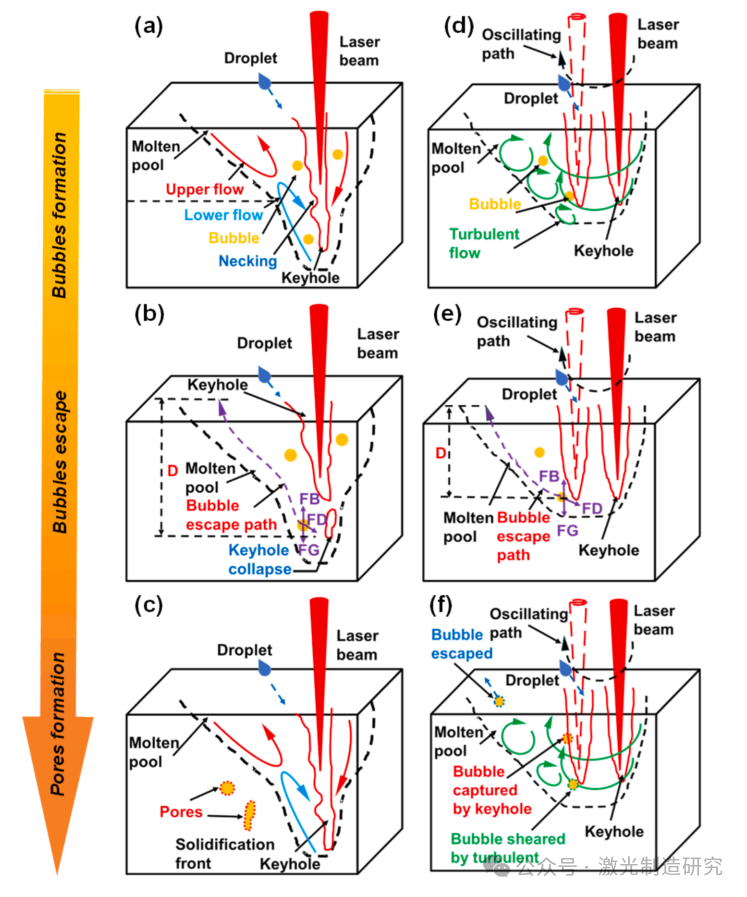
图12.电子束振荡对气孔形成的影响机制,(a-c)非振荡复合焊接,(d-f)具有优化振荡幅度的振荡复合焊接。
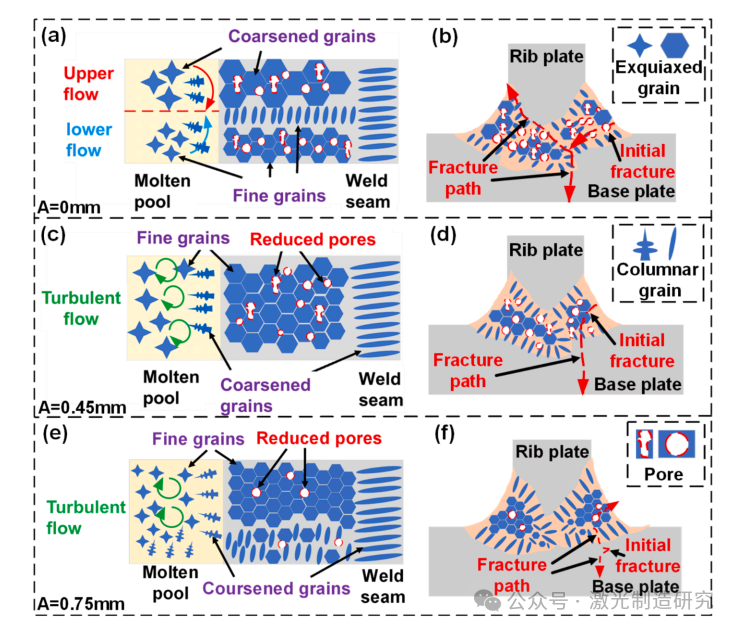
图13.振动振幅(A)对焊缝组织和拉伸断裂行为的影响机制,(a-b)A = 0 mm,(c-d)A = 0.45 mm,(e-f)A = 0.75 mm。
主要结论
(1).采用不同的激光振荡幅度A对6082铝合金T型接头进行激光-电弧复合焊接。
当A值为0.75 mm时,焊缝气孔率由9%降低到0.4%,可见的工艺气孔消失;随着A值的增加,焊缝熔深由11.87 mm降低到7.17 mm,上下熔区熔深差减小了45%。过渡角由129.2 °增大到178.8 °。
(2).优化后的激光振荡使焊缝组织均匀性提高了1.7倍,焊缝中心晶粒尺寸细化了29%,接头抗拉强度达到242 MPa,这比非政府组织高出30%,通过优化激光振荡,将拉伸断裂的起始位置从焊缝中心转移到热影响区。
(3).激光振幅对T型接头复合焊接的改善机理为:1.优化后的激光振幅提高了激光小孔的稳定性,激光振荡抑制了工艺气孔的形成,激光小孔对熔池的搅拌作用增强,有利于气泡的捕获,改善了焊缝组织的分布,细化了焊缝组织中的晶粒,提高了焊缝的性能。
主要信息
Effect of beam oscillating amplitude on formation characteristics and mechanical properties of laser-arc hybrid welded 8-mm-thick aluminum alloy T-joints
https://doi.org/10.1016/j.optlastec.2025.112676