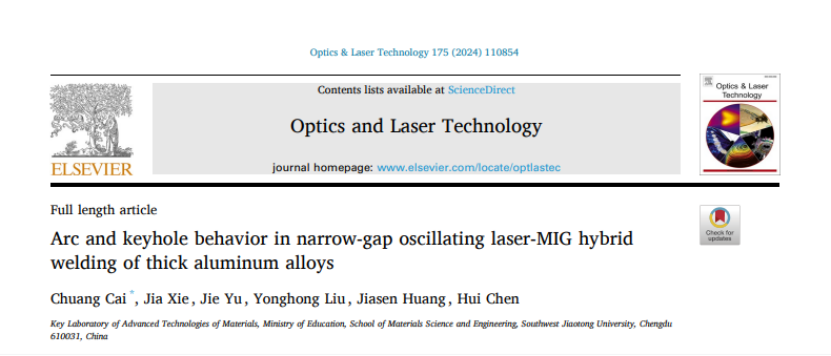
来自西南交通大学的学者在Optics & Laser Technology上发表了Arc and keyhole behavior in narrow-gap oscillating laser-MIG hybrid welding of thick aluminum alloys。
01 引言
厚板铝合金因高比强度和优良耐腐蚀性在多领域有广阔应用前景,但焊接是其结构制造关键技术。窄间隙激光 - MIG 复合焊接优势明显,不过铝合金激光 -MIG焊接中电弧和匙孔行为复杂,存在电弧偏转、小孔不稳定等问题,影响焊接质量。
02 全文概述
本文研究了窄间隙振荡激光-MIG复合焊接技术对于厚板铝合金的焊接,系统地探讨了不同振荡激光参数对焊缝成形及气孔缺陷的影响,并深入分析了电弧和匙孔动态行为对焊接质量的影响机制。研究表明:当送丝速度较高且振荡激光光斑直径小于3mm,激光振荡频率超过300Hz时,孔隙率可控制在0.5%以下,匙孔两侧穿透深度差异显著减小;当激光振荡频率处于300-450Hz、光斑直径为1-2mm,电弧燃烧稳定性增强,偏转角度减小,波动幅度降低,从而使得两侧壁穿透深度差异进一步缩小。此外,在振荡激光作用下,带电粒子数量增加并向上扩散至匙孔顶部区域,使电弧受到吸引而集中于匙孔底部中心位置,确保了电弧燃烧的稳定性以及两侧壁穿透深度的一致性。振荡激光对匙孔形成具有明显的抑制效果,不仅增大了匙孔开口尺寸,还降低了其波动程度。
03 图文解析
图1呈现不同激光功率下的焊缝表面和横截面形貌及两侧壁熔深差变化。直观展示了激光功率对焊缝成形的影响,如低功率时的未熔合现象、合适功率下的良好焊缝成形以及高功率时的表面不平整问题,反映了激光功率对焊缝成型和对称性的影响。
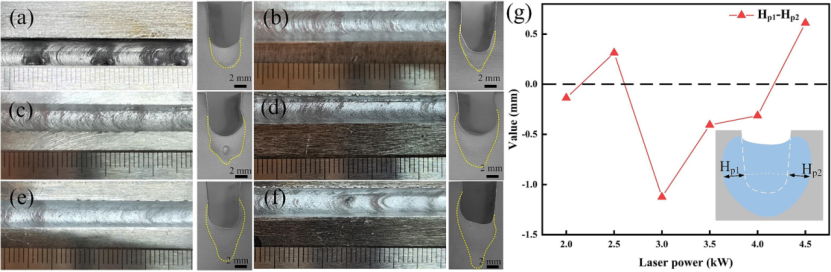
图1. 通过不同激光功率(P)获得的焊接表面和横截面形态以及两个侧壁贯穿之间的相应差异:(a) P = 2 kW,(b) P = 2.5 kW,(c) P = 3 kW,(d) P = 3.5 kW,(e) P = 4 kW,(f) P = 4.5 kW,(g) 两个侧壁之间的差异。
图2展示不同送丝速度下的焊缝表面和横截面形貌及两侧壁熔深差变化,清晰呈现送丝速度对焊缝成形的影响规律,即送丝速度增加,两侧壁熔深差减小,焊缝对称性增强。
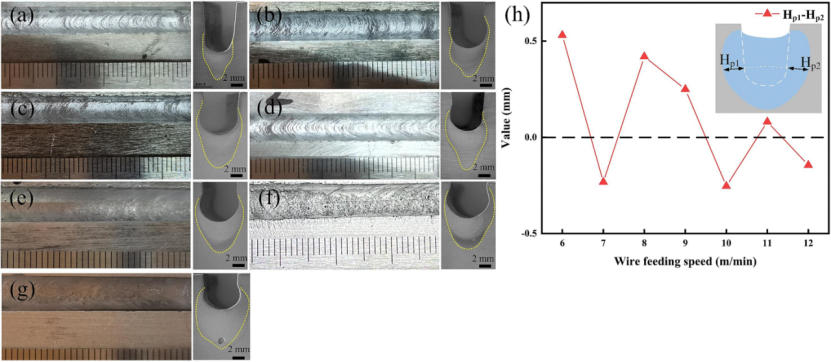
图2. 通过不同的送丝速度 (V) 获得的焊接表面和横截面形态以及两个侧壁穿孔之间的相应差异:(a) V = 6 m/min,(b) V = 7 m/min,(c) V = 8 m/min,(d) V = 9 m/min,(e) V = 10 m/min,(f) V = 11 m/min,(g) V = 12 m/min,(h) 两个侧壁之间的差。
图3呈现不同激光振荡频率下的焊缝表面和横截面形貌及两侧壁熔深差变化,表明振荡激光频率对电弧稳定性和两侧壁熔深差有显著影响,说明合适的振荡频率可优化焊缝成型。
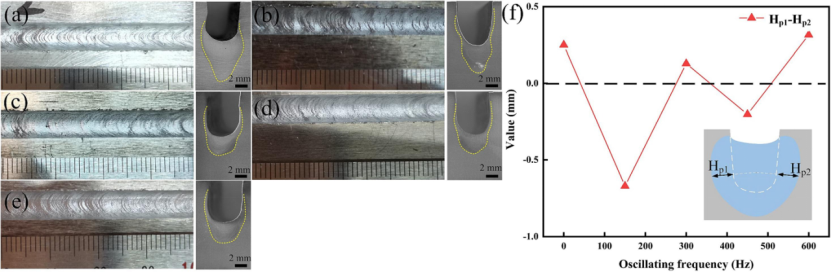
图3. 通过不同的激光振荡频率获得的焊缝表面和横截面形态:(a) R = 0 Hz,(b) R = 150 Hz,(c) R = 300 Hz,(d) R = 450 Hz,(e) R = 600 Hz,(f) 两个侧壁之间的相应差异。
图4展示了不同激光振荡直径下的焊缝表面和横截面形貌及两侧壁熔深差变化,振荡直径高于 2mm 时,焊缝表面鱼鳞纹更均匀。振荡直径增加,两侧壁熔深差先减小后增大,2mm 时电弧稳定,4mm 时电弧受激光束吸引发生偏转,导致两侧壁熔深差增大和焊缝不对称,表明振荡直径对电弧稳定性和焊缝成型有显著影响。
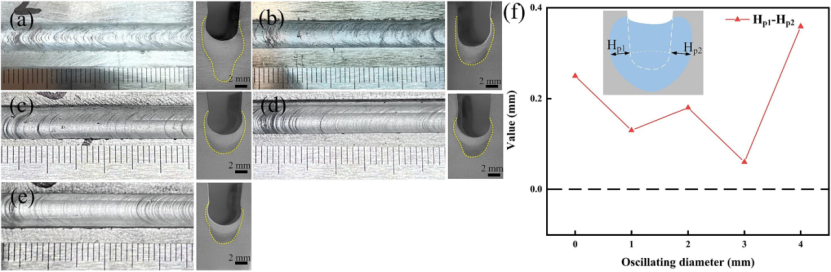
图4. 通过不同的激光振荡直径获得的焊缝表面和横截面形态:(a) Rd = 0 mm,(b) Rd = 1 mm,(c) Rd = 2 mm,(d) Rd = 3 mm,(e) Rd = 4 mm,(f) 两个侧壁之间的相应差异。
图5展示了不同焊接参数下的焊缝气孔率变化,直观呈现激光功率、送丝速度、振荡频率和振荡直径对气孔率的影响趋势,激光功率增加,气孔率上升;送丝速度增加,气孔率先增后减,10m/min 时气孔率最大为 4.1%;振荡激光可显著降低气孔率,频率高于 300Hz 时气孔率低于 0.5%,振荡直径在频率为 300Hz 时对气孔率影响较小,均低于 0.5%。
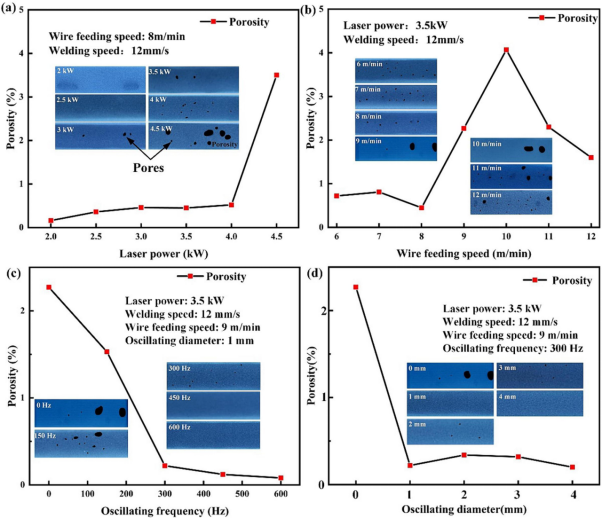
图5. 焊缝孔隙率随不同的焊接参数而变化:(a) 激光功率,(b) 送丝速度,(c) 振荡频率,(d) 振荡直径。
图6展示了不同焊接参数下的电弧行为和偏转角度,低激光功率时电弧燃烧不稳定、易被侧壁吸引,偏转角度和离散度大;高激光功率时电弧偏转角度减小,稳定性提高。低送丝速度时电弧易被侧壁吸引,焊缝不对称;高送丝速度时电弧稳定,偏转角度显著减小。
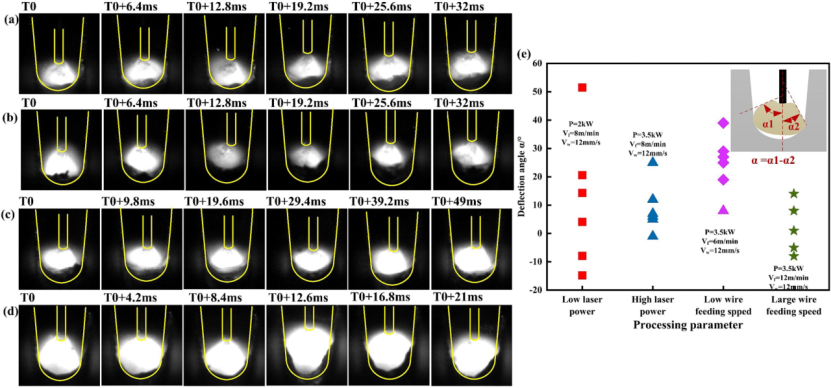
图6. 不同焊接参数的电弧特性和偏转角:(a) 低激光功率(P = 2 kW,V = 8 m/min,Vw = 12 mm/s),(b) 高激光功率(P = 3.5 kW,V = 8 m/min,Vw = 12 mm/s),(c) 低送丝速度(P = 3.5 kW,V = 6 m/min,Vw = 12 mm/s)(d) 大送丝速度(P = 3.5 kW, V = 12 m/min,Vw = 12 mm/s),(e) 电弧偏转角的散点图。
图7为不同激光振荡频率下的电弧行为和偏转角度及对应偏转角度散点图,振荡激光 - MIG 复合焊接时电弧燃烧稳定,450Hz 时电弧偏转角度显著减小,波动程度降低约 60.3%;600Hz 时电弧偏转角度波动更剧烈,说明振荡频率对电弧稳定性和偏转角度有重要影响。
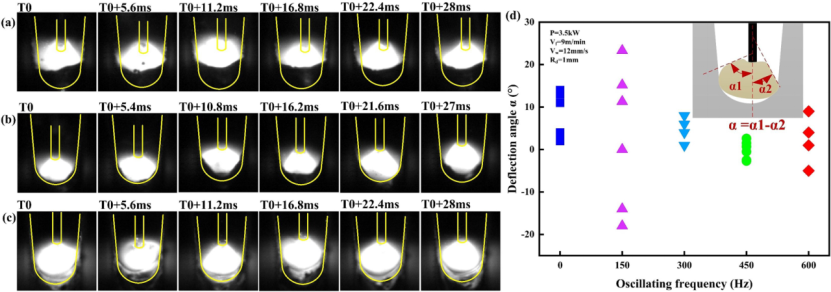
图7. 不同激光振荡频率的电弧行为和偏转角以及相应的偏转角:(a) R = 0 Hz,(b) R = 300 Hz,(c) R = 600 Hz,(d) 电弧偏转角的散点图。
图8为不同振荡直径下的电弧行为和偏转角度及对应电弧偏转角度散点图:振荡直径增加,电弧偏转角度先减小后增大,2mm 时电弧极稳定,4mm 时电弧偏转增大。
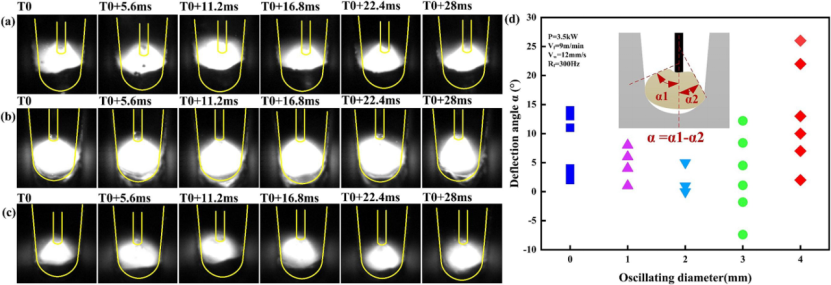
图8. 不同振荡直径的电弧行为和偏转角以及相应的电弧偏转角:(a) Rd = 0 mm,(b) Rd = 2 mm,(c) Rd = 4 mm,(d) 电弧偏转角的散点图。
图9为不同参数下的等离子体温度和密度,振荡直径为 1mm 时,激光振荡频率对等离子体温度影响小,但会显著降低等离子体密度;振荡直径高于 2mm 时,等离子体温度和密度均显著降低。
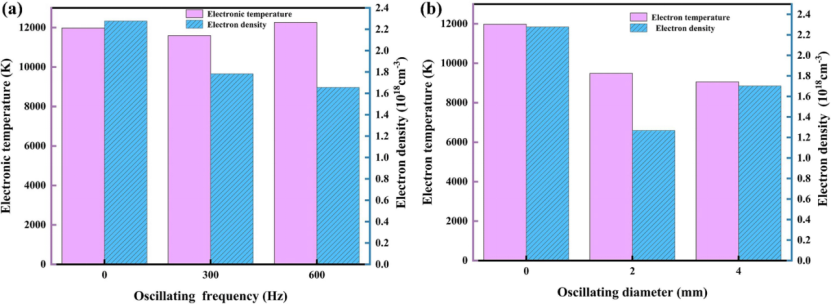
图9. 通过不同参数获得的等离子体温度和密度:(a) 激光振荡频率,(b) 激光振荡直径。
图10为等离子体分布对电弧行为影响的示意图,传统激光 - MIG 复合焊接时,电弧受侧壁吸引;振荡激光 - MIG 复合焊接时,电弧受激发电子吸引向坡口中心底部冲击。
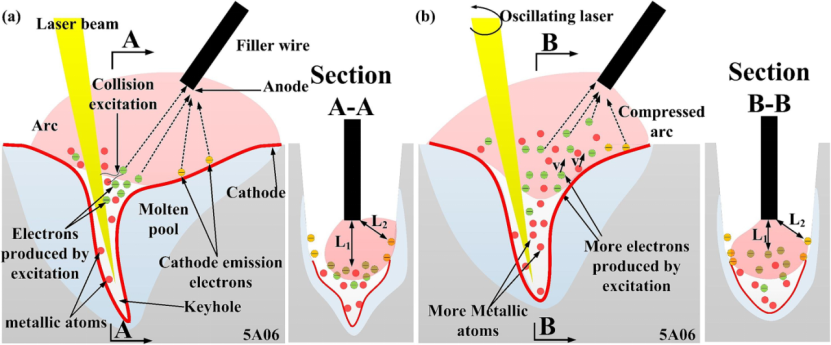
图10. 等离子体分布对电弧行为影响的示意图:(a) 常规激光-MIG 复合焊接,(b) 振荡激光-MIG 复合焊接。
图11在对于焊接过程中的小孔动态行为研究中,可以发现,传统焊接时小孔深度波动大(4.3 - 11.8mm),开口尺寸小(0.8 - 1.4mm);振荡激光 - MIG 复合焊接(频率 600Hz、直径 1mm)时小孔深度波动小(6.8 - 10.1mm),开口尺寸约为传统焊接的两倍且更稳定(2.3 - 3.8mm),表明振荡激光可改善小孔稳定性。
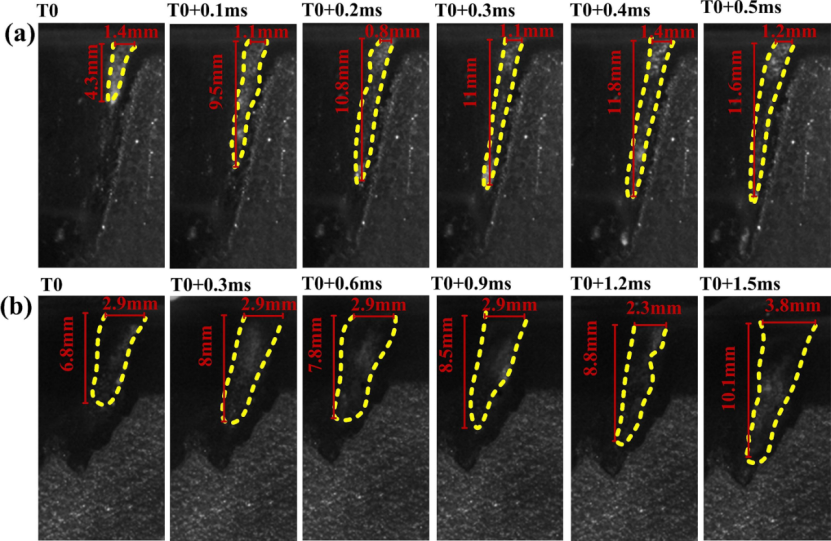
图11. 焊接过程中的锁孔动力学特性:(a) 传统的激光-MIG 复合焊接,(b) 振荡激光-MIG 复合焊接。
04 结论
本文结论如下:
(1) 降低激光功率、增加送丝速度和采用振荡激光有利于减小两侧壁熔深差;激光功率增加会使焊缝气孔率上升,振荡频率高于 300Hz 时气孔率显著降低。
(2) 电弧稳定燃烧并冲击坡口中心底部时,两侧壁熔深均匀;高送丝速度和合适的振荡激光参数(频率 300 - 450Hz、直径 1 - 2mm)利于电弧稳定燃烧。
(3) 振荡激光使激发电子增多并扩散到坡口上部,吸引电弧冲击坡口中心底部,可以抑制不对称焊缝形成。
(4) 焊缝气孔率与小孔动态行为相关,振荡激光 - MIG 复合焊提高了小孔稳定性,有利于抑制气孔缺陷。