
摘要
在本研究中,研究了 16 mm 厚 TC4 钛合金窄间隙激光电弧复合焊接中的焊缝成形、电弧行为和熔滴过渡。熔深主要受激光功率和焊接速度的影响,而填充金属高度和侧壁熔深则与送丝速度成正比。焊缝断面形貌可分为倾斜形、凹形和凸形三种。通过优化激光功率和送丝速度,电弧偏转角的标准偏差σ分别降低了约73.7%和77.9%。这表明电弧稳定性得到增强。将焊接速度从 14 mm/s 增加到 20 mm/s 导致 σ 增加约 343.6%,表明电弧稳定性减弱。当熔滴过渡偏离焊丝轴线时,会获得倾斜的焊缝。由于熔池表面中部过度会聚的熔融金属铺展不充分,形成凸焊缝。当会聚的熔融金属在熔池表面中部充分扩散时,就会产生凹形焊缝。
引言
钛合金以其高强度、低密度和优异的耐腐蚀性能而广泛应用于航空航天和海洋工程领域。钛合金厚板的焊接质量是影响上述领域大型装备使用性能的关键因素。钛合金具有很强的高温活性。在焊接过程中,保护不充分的钛合金容易发生氧化、氮化、脆化,从而降低焊接质量。Chen等人提出,氧化钛合金接头的机械性能显着下降。因此,在焊接过程中对钛合金进行保护就显得尤为重要。与传统的大角度坡口(45°≤坡口角度≤60°)相比,窄间隙厚板焊接具有残余应力小、焊接效率高等优点。钨极惰性气体保护焊(TIG)和熔化极气体保护焊(GMAW)广泛应用于厚板的窄间隙焊接。Wan等人对78 mm厚的TC4板进行窄间隙TIG焊接,获得了母材抗拉强度的91.2%。Reda等人[13]指出,采用低焊接电流产生的Ti-6Al-4V合金TIG焊接接头由于高冷却速率、低热输入和产生细晶粒而具有高抗拉强度和硬度。尽管窄间隙TIG焊接工艺稳定,但未熔合(LOF)缺陷仍然是一个关键问题[14]。与TIG焊相比,GMAW焊由于热输入大、焊接稳定性差,在钛合金厚板中的应用受到限制。通过使用填丝窄间隙激光焊接克服了窄间隙电弧焊的一些缺点,例如大的热影响区和热变形。Fang等人研究了10 mm厚TC4板的窄间隙激光填丝焊接。焊缝中心等轴晶区的平均晶粒尺寸随着热输入的增加而增大,热影响区软化。Xu等人指出,激光填丝焊接导致焊接区变得比母材更硬。然而,即使使用填充焊丝激光焊接,飞溅和气孔等其他问题仍然没有得到解决。
与激光焊或电弧焊相比,激光电弧复合焊(LAHW)具有桥接能力强、焊接效率高、焊缝成型好等优点。因此LAHW在厚板焊接中具有良好的应用前景。在窄间隙 LAHW (NG-LAHW) 过程中,激光和电弧以及窄间隙的空间约束效应导致复杂的电弧行为和熔滴转移。Cai等发现电磁和等离子体曳力是影响高强钢LAHW过程中熔滴传递的关键因素。龚等人[29]的结论是,由于空间约束效应,NG-LAHW 中的电弧等离子体面积更小,电弧膨胀-收缩过程比 LAHW 更稳定。李等人指出,随着电弧能量的增加,熔滴过渡模式从短路过渡转变为短路和喷射过渡的混合模式,最后变为喷射过渡。Ming等人认为侧壁上的LOF是NG-LAHW的主要缺陷。LOF 受前道横截面形状的影响,并被凹形形状有效抑制。尽管大量研究集中在钢和铝合金厚板的NG-LAHW上,但对钛合金厚板的NG-LAHW,特别是焊接稳定性关注较少。打底焊是多层多道焊的基础,对接头质量有重大影响。此外,NG-LAHW的稳定性直接受到激光功率(P)、送丝速度(Vf)和焊接速度(Vw)等工艺参数的影响。然而,钛合金厚板 NG-LAHW 工艺参数、焊缝成形和焊接稳定性之间的关系仍不清楚。在本研究中,NG-LAHW 打底焊在 16 毫米厚的钛合金上进行。观察并分析了电弧行为、熔滴过渡和熔池流动。进一步讨论了焊缝成形对焊接稳定性的影响,并阐明了LOF的形成机制。
实验设置
采用尺寸为80 mm×80 mm×16 mm的TC4钛合金板和直径为1.2 mm的ERTi-6Al-4V填充焊丝。焊接前,将板材打磨并用无水乙醇清洗,以去除氧化层和污染物。使用光纤激光器(TruDisk-10,002)和弧焊机(TransPuls Synergic 4000)。实验采用连续激光输出方式,最大激光功率为10 kW,激光波长为1070 nm,焦距为400 mm。焊接电流、电压与送丝速度自动匹配,采用脉冲直流模式。NG-LAHW 系统包括 ABB 机器人和集成操作柜。NG-LAHW实验装置和焊接工艺分别如图1(a)和(b)所示。使用特殊的防护装置将板固定在水平工作台上。激光束与垂直方向的夹角为10°,焊枪与板材的夹角为75°。激光束和焊丝尖端之间的距离为2mm。焊接电流电压采集系统的主要组成部分是NI采集卡和霍尔电流电压传感器。使用LabVIEW收集焊接电流和电压值。针对钛合金NG-LAHW设计了专用保护装置,采用99.99%高纯氩气作为保护气体,流量为50 L/min,如图1(c)所示。NG-LAHW焊接工艺参数、平均焊接电流和电压值列于表1。金相样品依次进行切割、研磨、抛光,并使用 5% HF + 25% HNO3 + 70% H2O 溶液进行蚀刻。使用ZEISS STEMI 2000显微镜观察焊缝的宏观形貌。选择熔深深度(HP)、填充金属高度(HF)和侧壁熔深(HS)作为焊接成型参数。使用高速相机 (Phantom v2512) 以 20,000 fps 的帧速率观察电弧行为、熔滴转移、小孔行为和熔池流动。高速相机系统采用高频脉冲激光器(CAVILUX HF)作为光源,如图2所示。图2(a)显示了用于观察位置1的高速相机。电弧行为和熔滴转移以及位置 2 用于观察熔池流动的情况。图2(b)显示了用于观察锁孔行为的“三明治”结构。将板放置在移动平台上并且热源的位置固定。使用AMC4030软件控制平台的步进距离和速度。
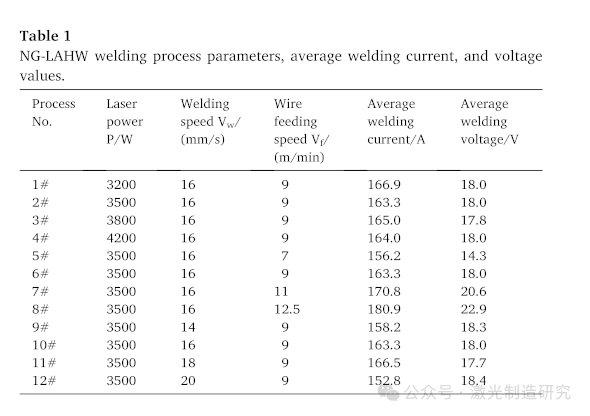
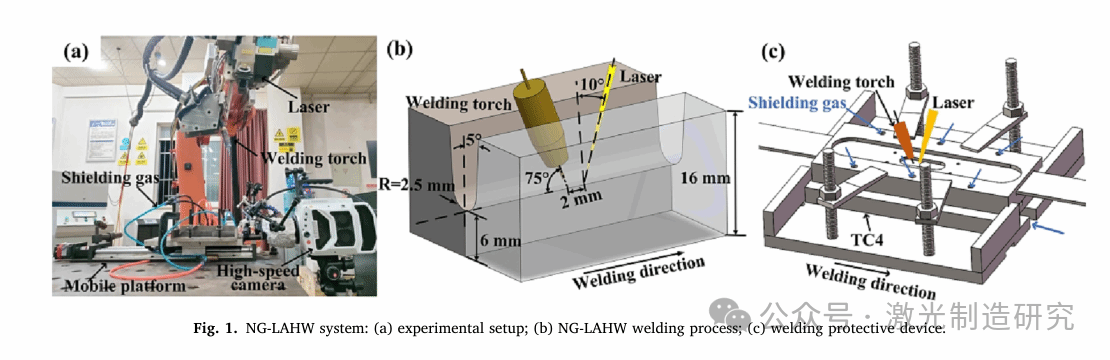
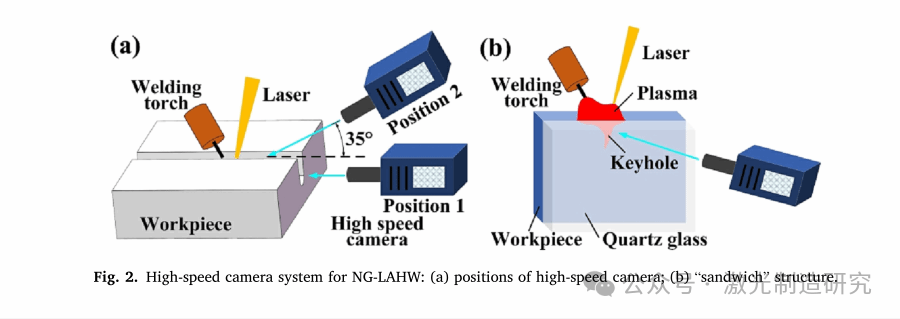
结果与讨论
图3为送丝速度9 m/min、焊接速度16 mm/s下不同激光功率下的焊缝表面形貌和截面形貌。在激光功率为3200 W时,形成倾斜焊缝,并在侧壁上观察到飞溅,如图3(a)所示。鱼鳞状分布均匀的凹形焊缝使用3500 W的激光功率获得图案,如图3(b)所示。焊缝没有飞溅和气孔。在3800 W和4200 W的激光功率下,产生凸焊缝,分别如图3(c)和(d)所示。在 4200 W 的激光功率下观察到间歇性的表面形成和孔隙。激光功率与焊缝成形参数之间的关系如图3(e)所示。穿透深度随着激光功率的增加而增加。激光功率为 3200 W 时,Hp 为 2.0 mm。与激光功率 3200 W 相比,激光功率为 4200 W 时,穿透深度增加了 2.5 mm。由于更高的热输入和更强的强度,获得了更大的穿透深度。较高激光功率下的穿透能力。此外,填充金属的高度随着激光功率的增加而缓慢增加。激光功率越高,高温液态金属蒸发越剧烈,熔池前面的熔融金属通过匙孔底部流入后面熔池时形成较大的顺时针涡流。这促进了液态金属的积累并导致填充金属高度更大,如图4所示。此外,由于侧壁熔深主要发生在电弧区域,并且受电弧能量的影响显着,因此侧壁熔深波动了约1mm。
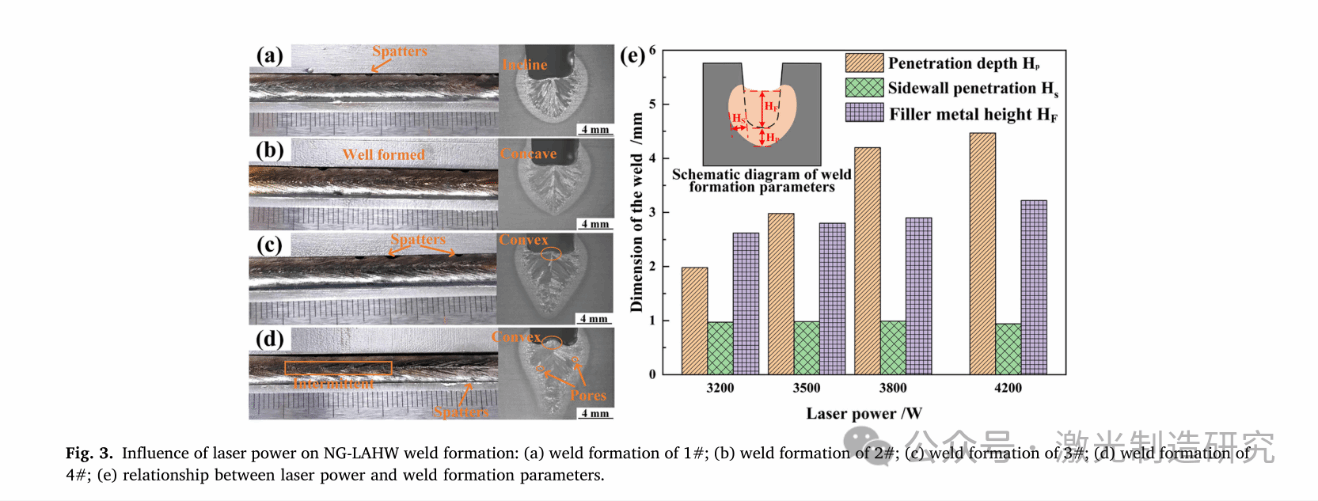
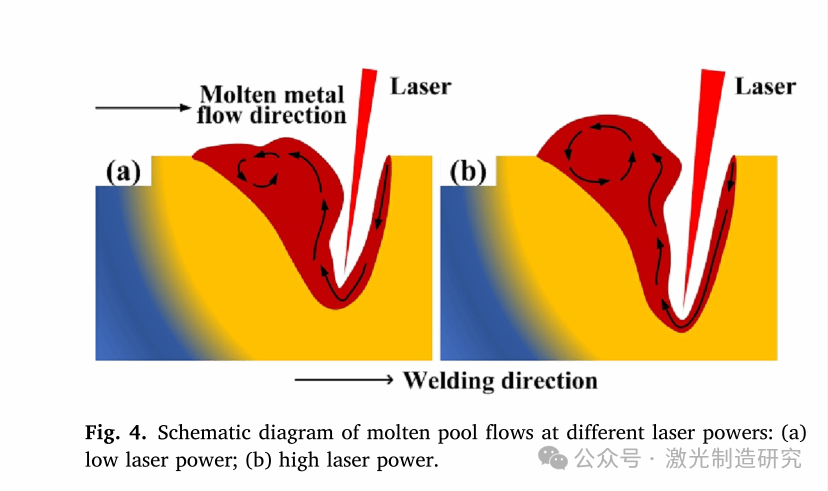
激光功率为 3500 W、焊接速度为 16 mm/s 时,不同送丝速度下的焊缝表面形貌和截面形貌如图 5 所示。送丝速度为 7 m/min 时,倾斜的焊缝形状如图 5 所示。观察到焊缝有气孔,焊缝表面形成断续,如图5(a)所示。在送丝速度为 11 和 12.5 m/min 时,获得了带有飞溅的凹形焊缝,分别如图 5(c)和(d)所示。以12.5 m/min的送丝速度在焊缝中观察到气孔。图5(e)显示了送丝速度和焊缝成形参数之间的关系。送丝速度12.5m/min时的Hp为3.0mm,比送丝速度7m/min时的Hp低25%。随着送丝速度的增加,焊接电流增加,从而导致金属蒸气增加。此外,金属蒸气增强的激光屏蔽效应导致Hp降低。此外,沉积在基材上的熔融金属量随着送丝速度的增加而增加。激光穿过熔融金属时消耗的能量增加,减少了施加到基材上的激光能量,导致穿透深度更小。HF随着送丝速度的增加而增加,在送丝速度为12.5 m/min时达到最大值3.5 mm。这种现象归因于单位时间内熔化的焊丝量增加。当送丝速度从7变为12.5 m/min时,Hs从0.9增加到1.5 mm。这表明侧壁熔深随着送丝速度的增加而逐渐增加。较高的送丝速度导致较高的焊接电流,因此,侧壁的热量输入较大。
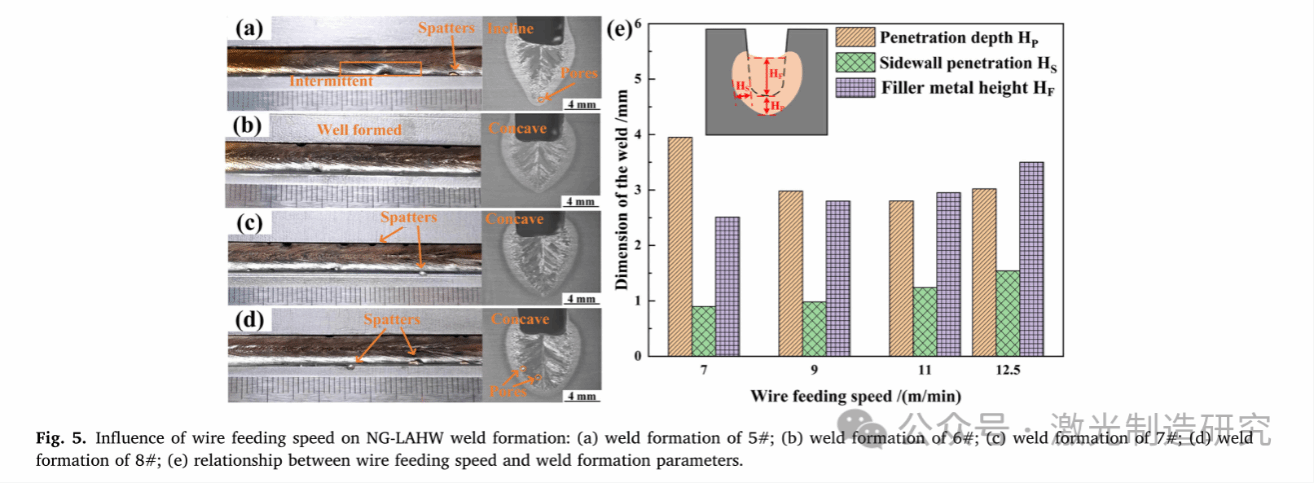
不同焊接速度、激光功率为 3500 W、送丝速度为 9 m/min 时的焊缝表面形貌和截面形貌如图 6 所示。焊接时获得了具有良好表面形貌的凹焊缝。速度为14毫米/秒。然而,在焊缝中观察到一些气孔,如图6(a)所示。在18mm/s的焊接速度下,形成了具有断续表面结构的倾斜焊缝,如图6(c)所示。焊接速度为20mm/s时,得到带有飞溅的凸焊缝,如图6(d)所示。图6(e)显示了焊接速度对焊缝成形参数的影响。随着焊接速度的增加,Hp、HF和Hs降低。焊接成形参数的这种变化与焊接能量有关。激光电弧复合焊接能量由下式给出

其中Q表示混合焊接能量,U表示平均焊接电压,I表示平均焊接电流,P表示激光功率,v表示焊接速度。对于恒定的激光功率和送丝速度,混合焊接能量随着焊接速度的增加而降低。当焊接速度为20 mm/s时,复合焊接能量为315.6 J/mm,比14 mm/s时降低约30.9%。因此,在较高的焊接速度下可以获得较小的熔深、填充金属高度和侧壁熔深。
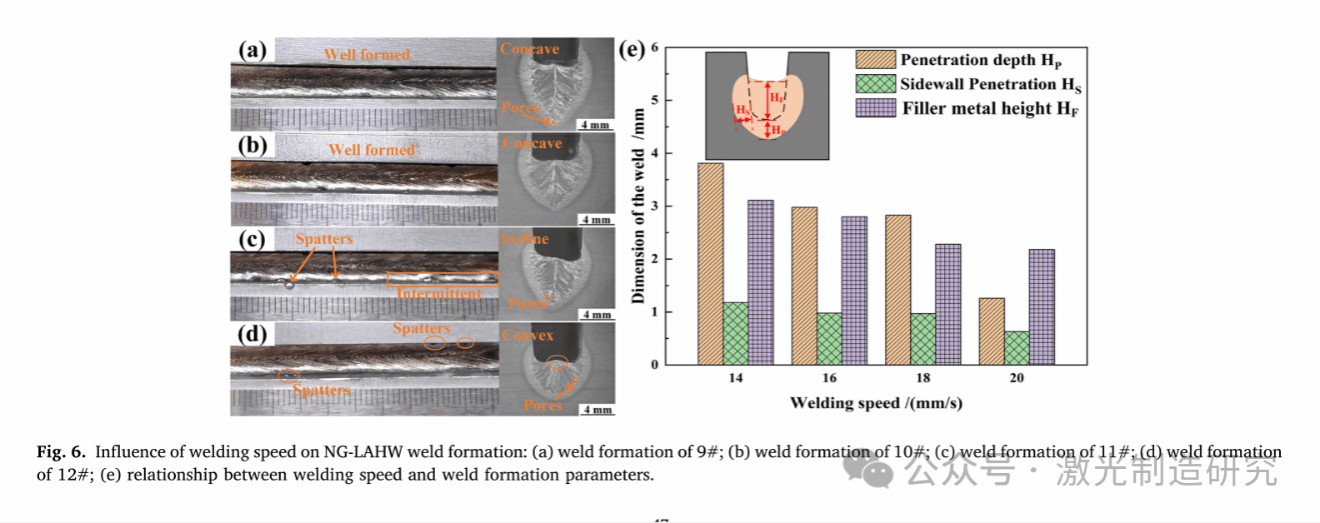
电弧行为是影响 NG-LAHW 焊接稳定性的关键因素。因此,研究焊接工艺参数对电弧行为的影响至关重要。为了表征电弧偏转程度,测量了脉冲峰值处的电弧偏转角α,如图7所示。由于电弧偏转角波动较大,表现出不稳定的电弧行为,因此采用标准差σ来表征电弧偏转角α。电弧偏转角波动:

式中,αi为电弧偏转角,α为平均电弧偏转角,n为电弧偏转角个数。
不同激光功率、焊接速度为 16 mm/s、送丝速度为 9 m/min 时的电弧行为和电弧偏转角如图 7 所示。激光功率为 3200 W 时电弧稳定性较差,原因是到圆弧偏转,如图7(a)所示。激光功率为3500 W时,侧壁对电弧的吸引力减弱,电弧形状变得更加规则,如图7(b)所示。在4200 W的激光功率下观察到形状规则的稳定电弧燃烧,如图7(c)所示。图7(d)显示,随着激光功率从3200 W增加到4200 W,σ从9.61减少到2.52。这相当于电弧偏转角减少了大约73.7%波动和增强的电弧稳定性。如表1所示,不同激光功率下的平均焊接电流和电压分别在165 A和18.0 V左右波动。这些结果表明焊接电流和电压仅受激光功率的轻微影响。因此,电弧稳定性主要受激光诱导等离子体的影响。激光诱导等离子体由于电离能低,增强了电弧燃烧的电通道,显着降低了起弧难度。根据最小电压原理,电弧消耗尽可能小的能量[33]。在较高激光功率下通过大量激光诱导等离子体增强电通道意味着电弧燃烧所需的能量更少。因此,观察到稳定的电弧燃烧。
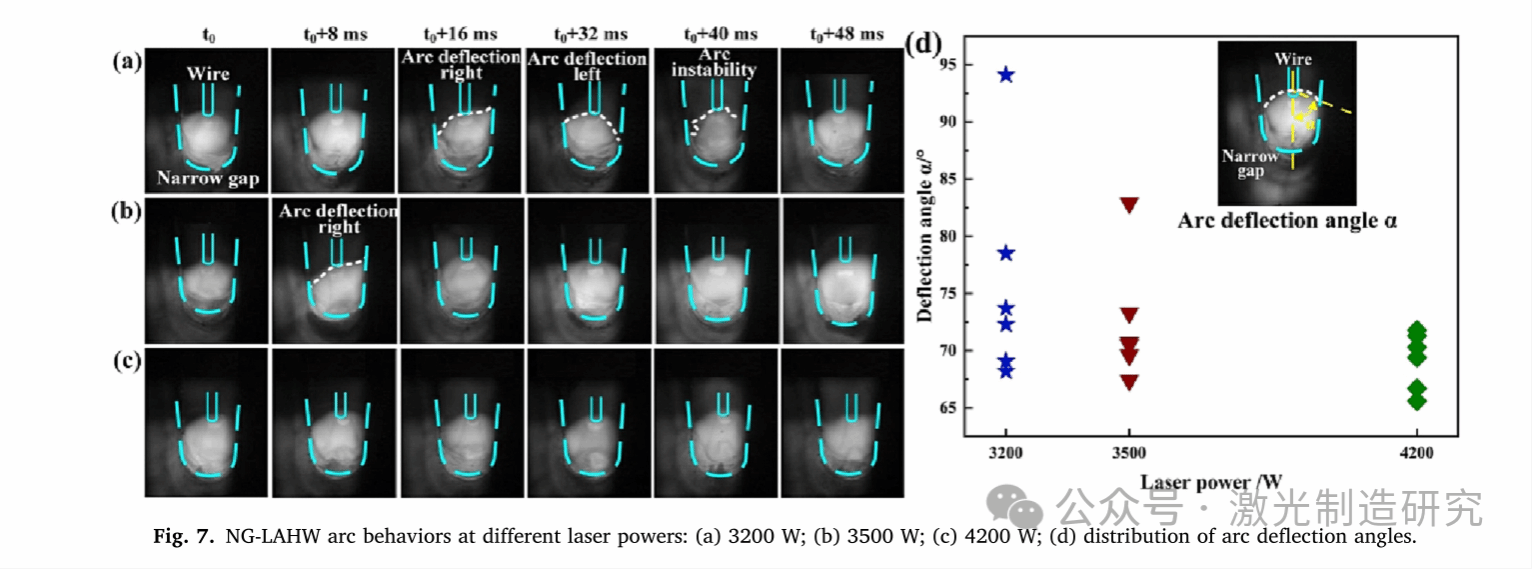
图8显示了不同送丝速度、激光功率为3500 W、焊接速度为16 mm/s时的电弧行为和电弧偏转角度。在较高的送丝速度下,电弧偏转得到抑制,电弧稳定性得到增强。在送丝速度为7 m/min时,电弧被侧壁吸引,电弧形状不规则,如图8(a)所示。由图8(c)可知,送丝速度为12.5 m/min时,电弧形状规则,未出现电弧偏转,表明电弧燃烧稳定。值得注意的是,随着送丝速度从 7 增加到 12.5 m/min,σ 从 15.54 下降到 3.42。电弧偏转角的波动减少了约77.9%,电弧稳定性增强,如图8(d)所示。如表1所示,平均焊接电流随着送丝速度的增加而增加。由于较高的送丝速度和较高的焊接电流,电弧刚度变得更强。因此,电弧偏转受到抑制,电弧燃烧稳定。
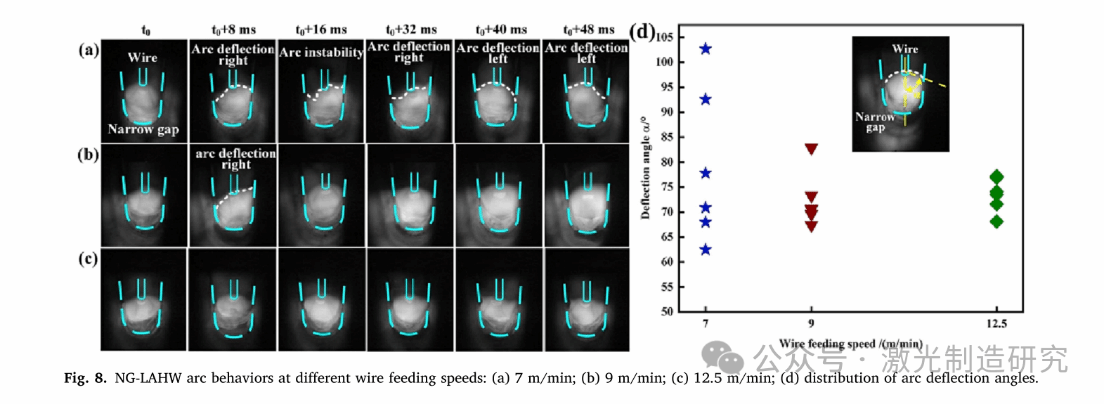
不同焊接速度、激光功率为3500 W、送丝速度为9 m/min时的电弧行为和电弧偏转角度如图9所示。焊接速度为14 mm/s时,实现了稳定的电弧燃烧,如图9(a)所示。相反,在焊接速度为20mm/s时,电弧燃烧不稳定,电弧形状不规则,如图9(c)所示。值得注意的是,随着焊接速度从 14 mm/s 增加到 20 mm/s,σ 从 3.07 增加到 13.62。这表明电弧偏转角的波动增加了约343.6%,电弧变得不太稳定,如图9(d)所示。这种现象归因于激光诱导等离子体从小孔的喷射方向。图 10 显示了不同焊接速度下的小孔行为和激光诱导等离子体。图10(a)显示,在14mm/s的焊接速度下观察到更深的小孔。激光诱导等离子体被小孔限制并沿着恒定方向稳定地喷射。形成稳定的电通道,电弧燃烧稳定。如图10(b)所示,由于焊接能量较低,在20mm/s的焊接速度下获得了较浅的小孔。小孔对激光诱导等离子体的约束减弱,激光诱导等离子体不会沿恒定方向喷射。电弧受到小孔喷出的激光诱导等离子体的冲击,削弱了电弧的稳定性。此外,在激光诱导等离子体的喷射方向上形成了电通道,这导致电弧朝该方向偏转,并且在高焊接速度下电弧燃烧变得不稳定。
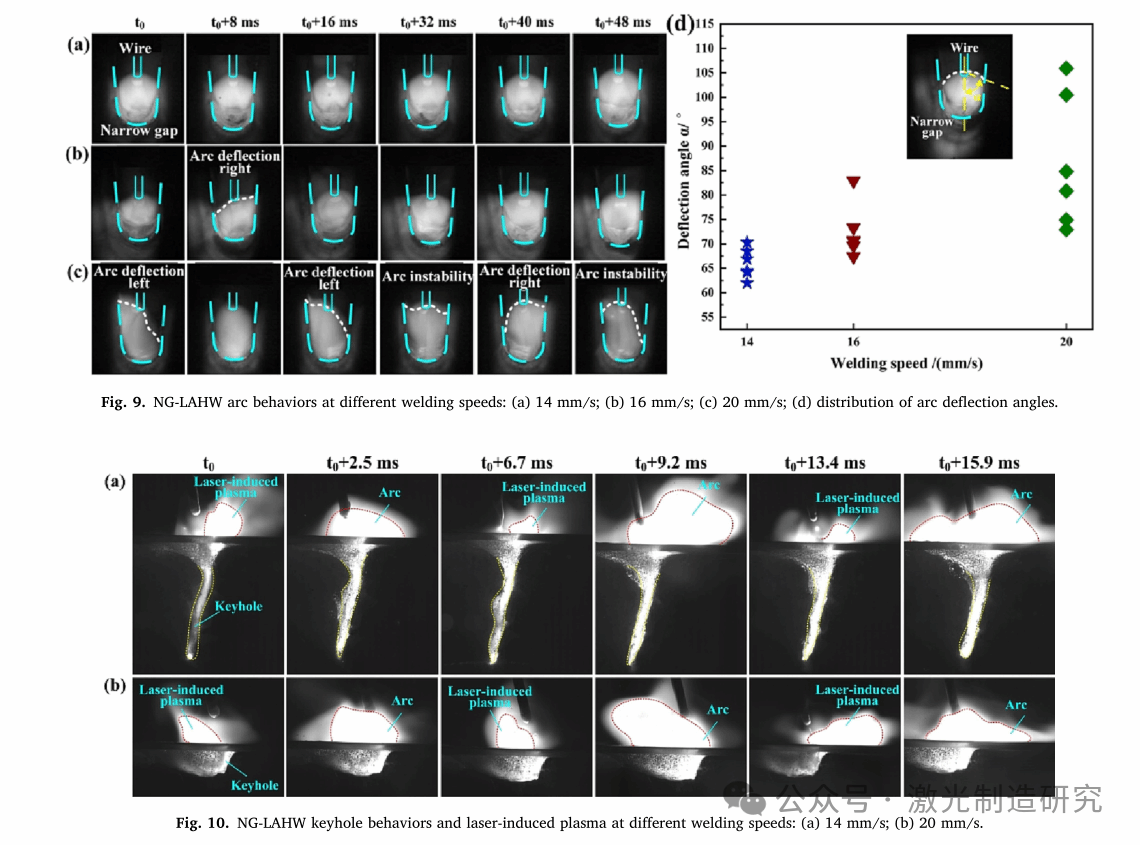
NG-LAHW 工艺期间电弧行为对熔滴过渡的影响会导致不同的焊接成型参数。因此,观察不同的熔滴过渡行为,以分析其焊接稳定性和焊缝成形。焊丝尖端熔化,通过电弧和激光的作用形成熔滴。当促进熔滴过渡的力超过阻碍熔滴过渡的力时,熔滴从焊丝上脱离,以球状形式落入熔池中。液滴主要受重力(Fg)、等离子体流动力(Fp)、表面张力(Fσ)、电磁力(Fem)和金属蒸气反冲力(Fv)的影响。Fg、Fp 和 Fem 促进液滴转移,而 Fσ 和 Fv 阻碍液滴转移。此外,关键力Fem和Fp影响液滴转移及其方向。Fem 由给出

其中 μem 是自由空间的磁导率,I 是焊接电流,fem 是几何系数。Fem 与焊接电流成正比,而 Fem 和 Fp 的方向由电弧决定。
图11显示了高送丝速度(12.5 m/min)下的熔滴转移过程。在图11(a)和(d)中,在坡口中心产生电弧,在焊丝尖端形成熔滴。电流线从液滴指向凹槽中心,Fp和Fem都指向凹槽中心。在Fp、Fem和Fg的共同作用下,熔滴从焊丝尖端脱离并落入熔池中,如图11(b)和(e)所示。具体而言,在 180.9 A 的较高焊接电流下,熔滴获得了较高的 Fem。熔滴冲击导致熔池表面严重凹陷和飞溅,观察到熔池剧烈波动,如图11(c)和(f)所示。这些剧烈的波动降低了小孔的稳定性并导致焊缝成型不良,如图 5(d)所示。
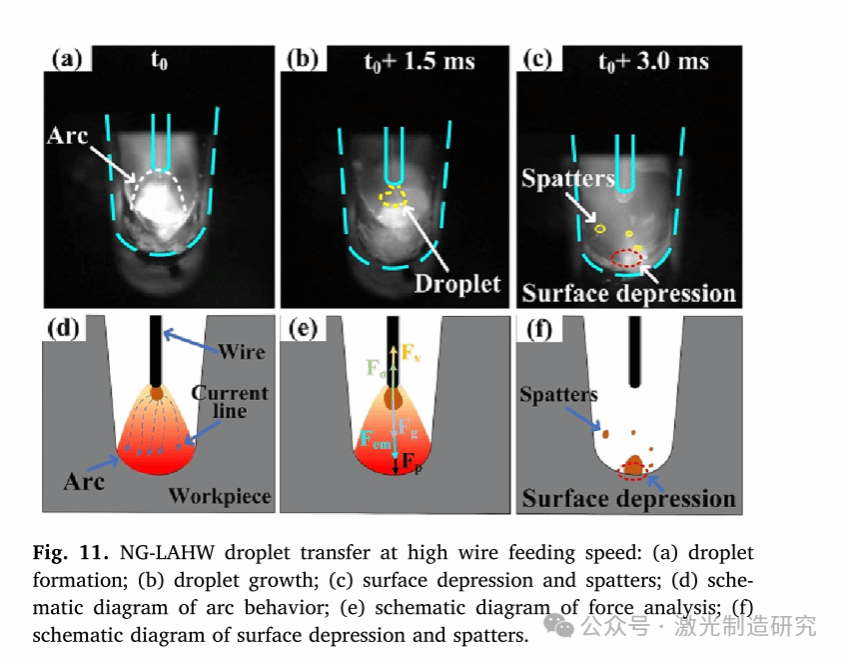
电弧偏转至侧壁时的熔滴过渡过程如图12所示。焊丝尖端与侧壁之间形成电通道,如图12(a)和(d)所示。液滴上Fp和Fem的方向随着电流线从液滴指向侧壁而偏转,如图12(b)和(e)所示。在Fp和Fem的共同作用下,熔滴过渡方向偏离焊丝轴线,指向侧壁。凹槽两侧的高度差是由于熔融金属在凹槽一侧的堆积造成的,如图12(c)和(f)所示。最终形成倾斜的焊缝,不利于后续道次的填充,如图1、2所示。图3(a)、5(a)和6(c)。
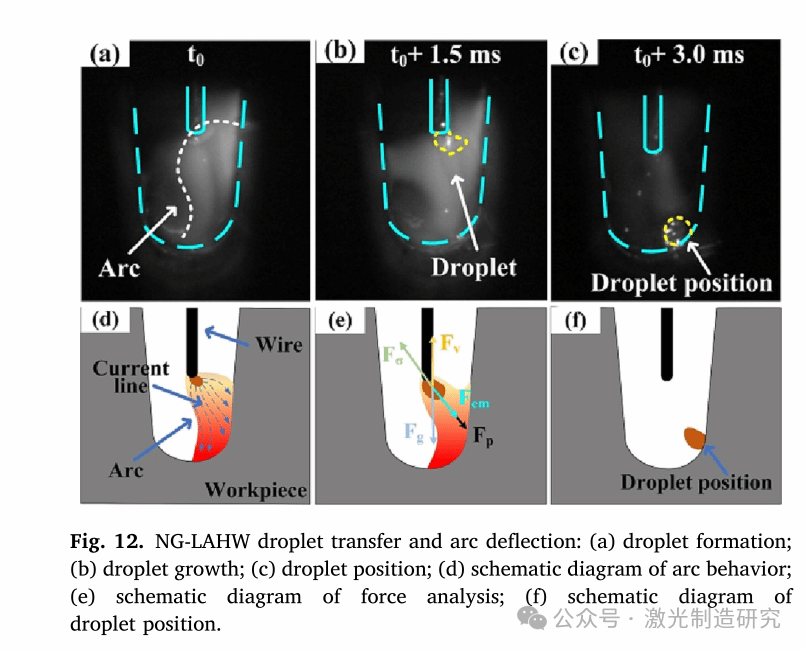
图 13 显示了激光功率为 3500 W、送丝速度为 9 m/min、焊接速度为 16 mm/s 时的熔滴过渡过程。如图13(a)和(d)所示,焊丝尖端和坡口中心之间形成电通道,熔滴和坡口中心之间形成电流线。Fem 和 Fp 指向凹槽中心。熔滴转移过程与高送丝速度下的相似,如图13(b)和(e)所示。然而,平均焊接电流比送丝速度 12.5 m/min 时的焊接电流低约 9.7%。由于较小的 Fem 作用于熔滴,因此没有观察到飞溅和熔池的轻微波动,如图 13(c)和(f)所示。在这种情况下,获得了成形良好的焊缝,如图3(b)所示。
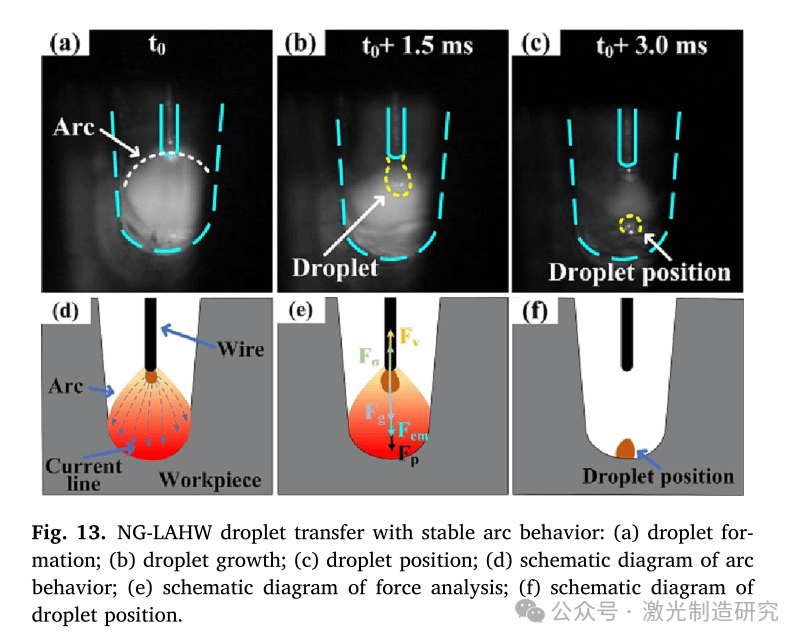
在这项研究中,获得了三种类型的焊缝横截面形貌。倾斜焊缝与熔滴过渡有关,而其他两种形态可归因于不同的熔池流动行为。因此讨论熔池流动与焊缝成形之间的关系是有意义的。图 14 显示了凹焊缝中的熔池流动。与LAHW相比,由于窄间隙的限制,NG-LAHW中的熔池流动更加复杂,可概括为四个阶段。在第一阶段,熔融金属流向两个侧壁,如图14(a)所示。第二阶段,熔融金属在狭窄间隙的限制下回流,如图14(b)所示。第三阶段,熔融金属在熔池表面中部汇聚,如图14(c)所示。在最后阶段,汇聚的金属液流向后方熔池并充分扩散到熔池两侧,如图14(d)所示。熔池流动示意图如图14(e)所示。凸焊缝中的熔池流动如图15所示。此时,熔融金属流动可分为四个阶段。然而,与凹焊缝相比,熔池流动存在一些差异。同样,熔融金属向两侧侧壁流动,回流,并在熔池表面中部汇聚,如图15(a)-(c)所示。然而,在第三阶段,大量的熔融金属聚集在熔池表面的中部。如图15(d)所示,观察到熔池表面中部有过多的熔融金属堆积。最后阶段,汇聚的金属液直接流向熔池后部,少量金属液向两侧扩散。因此,由于过度会聚的熔融金属在熔池表面中部的扩散不充分,形成了凸焊缝。熔池流动示意图如图15(e)所示。
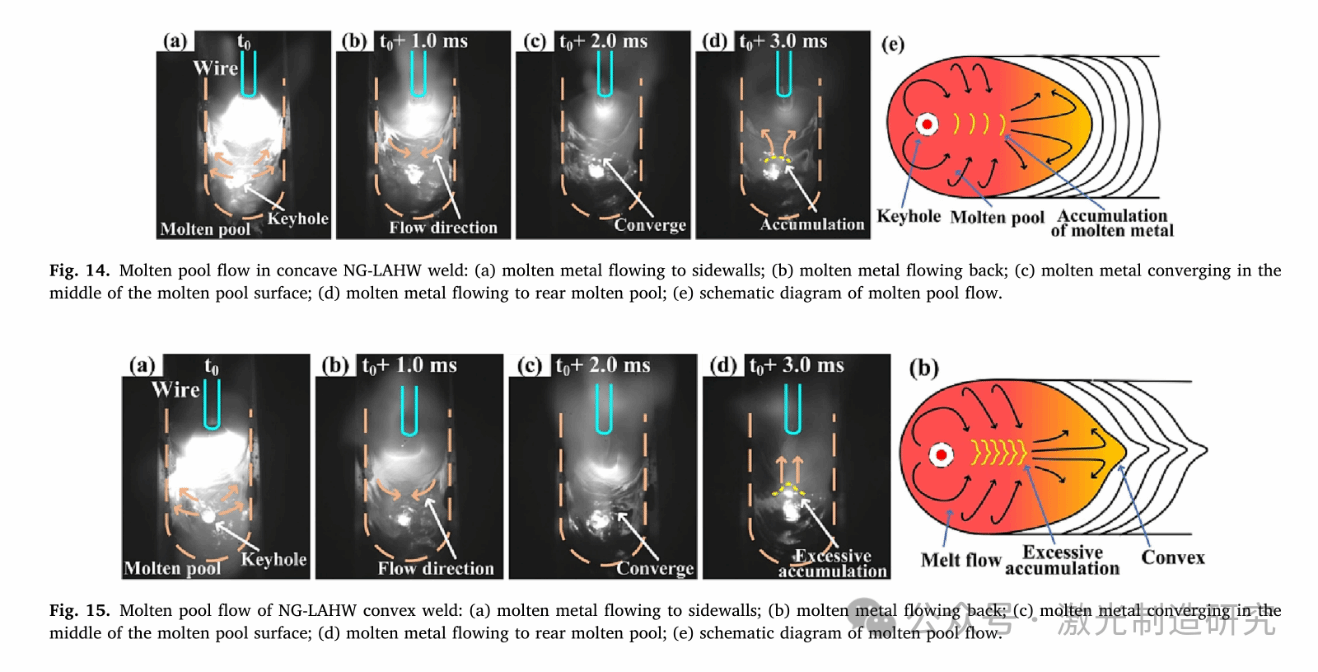
焊缝成形受焊接稳定性影响,LOF的发生与前道焊缝截面形貌密切相关。因此,阐明焊接稳定性、焊缝成型和 LOF 之间的关系非常重要。如图16(a)所示,焊丝尖端与坡口中心之间形成了电气通道,电弧燃烧稳定。槽底和侧壁充分加热并同步熔化。同时,熔滴在Fp和Fem的作用下沿焊丝轴线方向转移到熔池中。汇聚的熔融金属流向后方熔池并充分扩散。最后形成无尖角的凹形焊缝,有利于后续焊道的填充。当电弧被侧壁吸引时,电弧偏转一侧的母材被充分加热,而另一侧的母材则加热不足,如图16(b)所示。在Fp和Fem的作用下,熔滴沿电弧偏转方向从焊丝尖端脱离到熔池中。因此,由于熔融金属在一侧堆积,从而阻碍了后续道次的填充,从而形成具有尖角的倾斜焊缝。图16(c)显示了熔池流动、凸焊缝和LOF之间的关系。在熔池流动的第三阶段,多余的熔融金属汇聚在熔池表面的中部。最后阶段,汇聚的金属液直接流向后方熔池,扩散不充分。最后,产生了带有尖角的凸焊缝。尖角未完全受热熔化并充满熔融金属,两侧壁上形成LOF缺陷。
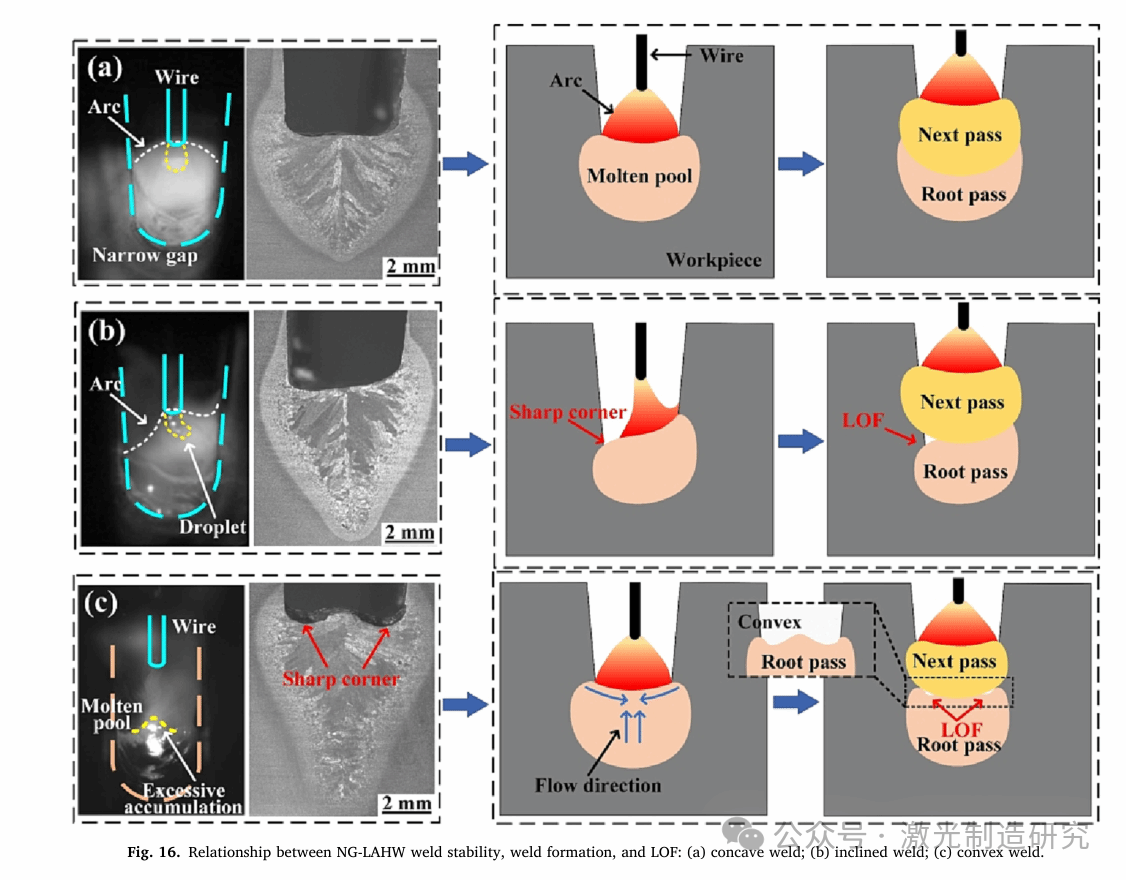
结论
本研究对厚度为16 mm的TC4钛合金进行NG-LAHW打底焊。研究了电弧行为、熔滴过渡和熔池流动。进一步讨论了焊接稳定性对焊缝成型的影响,明确了焊接稳定性、焊缝成型和LOF之间的关系。得出以下结论:
(1)焊缝断面形貌可分为倾斜型、凹型和凸型三种。熔深深度受激光功率和焊接速度的显着影响。填充金属高度和侧壁熔深与送丝速度成正比。
(2) 随着激光功率从3200 W增加到4200 W、送丝速度从7 m/min增加到12.5 m/min,电弧偏转角的标准偏差σ分别降低了约73.7 %和77.9 %。随着焊接速度从 14 mm/s 增加到 20 mm/s,σ 增加了约 343.6%。
(3)送丝速度较高时,熔池表面凹陷严重,飞溅严重。由于当电弧被吸引到侧壁时,熔滴过渡偏离焊丝轴线,因此形成倾斜焊缝。
(4)由于狭缝的限制,金属液回流并汇聚在熔池表面中部。当熔池表面中部过度会聚的熔融金属流向后方熔池且扩散不充分时,产生凸焊缝。当会聚的熔融金属在熔池表面的中部充分扩散时,就获得了凹形焊缝。
论文信息
Weld formation, arc behavior, and droplet transfer in narrow-gap laser-arc hybrid welding of titanium alloy
https://doi.org/10.1016/j.jmapro.2023.02.022